What is a magnetic type level gauge?
A magnetic Level Gauge is also called a magnetic level indicator. Magnetic Level Gauge is developed based on the principle of buoyancy and magnetic effect. The magnetic float in the measuring cylinder drives the two-color turning column on the external display of the measuring cylinder to flip with the increase (decrease) of the liquid level to be measured. As the position of the float changes, the indicator moves up and down the same amount. Supports top-mounted and side-mounted. It can be used for liquid level detection in high temperature, low temperature, high pressure, strong corrosion, highly toxic and dangerous environments.
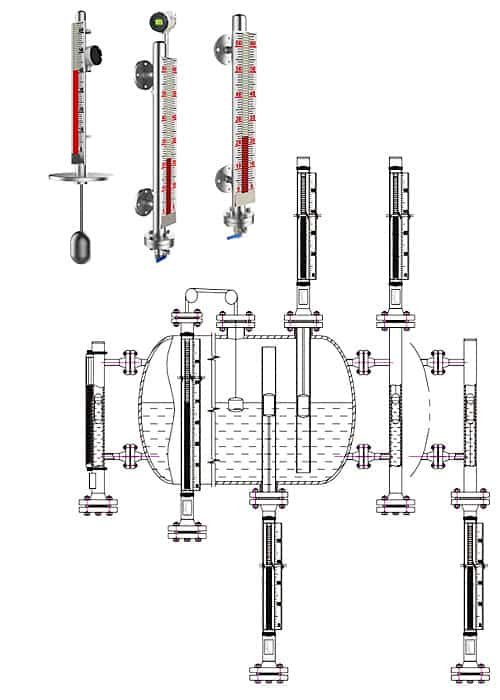
The parts and components of Magnetic Level Gauge are made of 304, 321, 316L, 1Cr18Ni9Ti, 00Cr17Ni14Mo2, 0Cr18Ni9, 304 or 0Cr18Ni9 lined with PTFE (polytetrafluoroethylene), PVC, PP, and other materials. And imported high-quality electronic components. The product has high reliability, good stability, long-lasting durability, and strong corrosion resistance.
Its characteristics are very significant:
Still have questions?
If you cannot find an answer to your question in our FAQ, you can always contact us
and we will be with you shortly.
More Featured Level Gauges/Indicators
Based on the product selection, we can determine the price of the level transmitter. Sino-Instrument is a manufacturer of level transmitters, so we offer the best price.
For example: The reference price of a differential pressure level transmitter is around USD 400.
Request a Quote
Wu Peng, born in 1980, is a highly respected and accomplished male engineer with extensive experience in the field of automation. With over 20 years of industry experience, Wu has made significant contributions to both academia and engineering projects.
Throughout his career, Wu Peng has participated in numerous national and international engineering projects. Some of his most notable projects include the development of an intelligent control system for oil refineries, the design of a cutting-edge distributed control system for petrochemical plants, and the optimization of control algorithms for natural gas pipelines.