Tank Level Measurement is important for industry storage tank. For example, level measurement of fuel oil tanks and the interface measurement of chemical storage tanks. The liquid level sensor is a kind of level instrument. Hydrostatic, Ultrasonic, Magnetostrictive, Radar, Differential Pressure are commonly choices for tank level measurement. Here, we mainly analyze the magnetostrictive liquid level sensor in the tank applications.
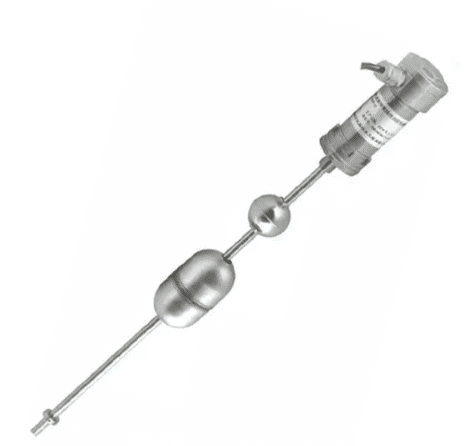
Liquefied petroleum gas is one of the most widely used fuels in civil and industrial production. During the storage and transportation of liquefied petroleum gas, liquid level measurement is an important task of the project. It is required not only to have high accuracy for liquid level measurement. It must also be able to adapt well to the working conditions of closed pressure vessels. At the same time, in order to meet the needs of remote monitoring and management. It must also require the measurement data to have the function of long-distance transmission.
Featured Level Sensors for Tank Level Measurement
Comparison of the common detection methods for the Tank Level Measurement
Instrument name | Accuracy | Measuring principle | Liquid level, interface, temperature measurement | Regular maintenance | On-site installation | overall costs | Service life |
---|---|---|---|---|---|---|---|
Magnetostrictive liquid level sensor | 0.5mm | Magnetostriction | Yes (integrated) | Maintenance-free | Simple | Low | 20 years |
Servo level sensor | 1mm | mechanical | Yes (split) | Regular maintenance | Complicated | High | short |
Guided wave radar level senosr | 1mm | Radar | no | Maintenance | Complicated | High | Longer |
Liquid level measurement methods for Tanks
There are 7 main types of level transmitters that Sino-Inst offers for Tank Level Measurement. Each type of transmitter works in a different way, and makes it useful for different types of processes.
- Capacitance Level Transmitters
- Hydrostatic Level Transmitters
- Magnetic Level Transmitters
- Radar Fill Level Transmitters
- Ultrasonic Level Transmitter
- Guided Microwave Level Transmitters
- Magnetostrictive Liquid Level Transmitters
Extended reading: Industrial Tank level indicators and Tank Level Gauges
Analysis and comparison with other level sensors
(1) Optical fiber level gauge
Based on optical technology. Use optical fiber as the sensor unit. Take out the sensitive state as an optical signal. Then photoelectric conversion. So it is easy to match with highly developed electronic control devices.
Compared with other conventional sensors, optical fiber sensors have high sensitivity, fast response speed, and strong resistance to electromagnetic interference. Corrosion resistance, good electrical insulation, small size and easy to form a remote monitoring network with optical fiber transmission system. Especially in the harsh environment of flammable and explosive, it is widely used.
(2) Differential pressure level gauge.Differential pressure level gauges use the principle of liquid pressure. At the bottom of the liquid, check the pressure difference between the liquid pressure and the standard atmospheric pressure. It deforms the semiconductor diffusion silicon film through the pressure of the liquid bottom.
Cause the bridge to be unbalanced. The circuit outputs a voltage corresponding to the liquid level height. In order to obtain the liquid level signal. It has the characteristics of high precision (0.7%), small drift and strong anti-overload capability.
But when the density of the medium changes with the temperature, pressure and composition of the medium, the differential pressure level gauge will produce a false level.
Extended reading: Hydrostatic Level Measurement
(3) Servo level gauge.
The servo liquid level gauge controls the float to follow the liquid level or interface changes through the servo motor. The servo float level gauge is subjected to different buoyancy forces on the liquid surface, in the liquid and on the interface through the float.
The gravity sensor is used to measure the weight of the float. It can send out long-distance signals at the same time. Use microcomputer for remote control. Its dynamic tracking error can reach 0.1mm.
At the same time, it can also compensate for the additional weight error caused by the low liquid level. The measurement accuracy of the liquid level can reach 0.7mm. The sensitivity can reach 0.1mm.
In addition, it also has self-diagnosis and communication functions. The level gauge has high reliability. But the price is relatively high.
(4) Radar level gaugeThe use of radar waves to measure the liquid level is a technology that has been paid close attention at home and abroad in recent years. It uses a horn-shaped waveguide to emit low-power microwaves (tens of microwatts).
Extended reading: Radar Oil Tank Level Sensor
After encountering the tested interface, part of the microwave is reflected back. Received by the transmitter and receiver combination level gauge system. Indirectly measure the liquid level by measuring the time difference between transmission and reception.
The biggest feature of the radar level gauge is that it is suitable for the environment where the application effect of the ultrasonic level gauge is not ideal.
Its maximum range can reach 35m, and the measurement accuracy can reach millimeter level. But its disadvantage is that the price is too high. Can not withstand high temperature and high pressure.
Read more about: 7 Level Senors for Tank Level Measurement
We can learn more about Fluid Level Measurement Techniques: https://www.azosensors.com/article.aspx?ArticleID=1097
Advantages of stainless steel magnetostrictive level sensor for oil Tank Level Measurement:
- High precision: the magnetostrictive liquid level gauge uses waveguide pulse to work. During the work, the measured displacement is determined by measuring the time of the start pulse and the end pulse. Therefore, its measurement accuracy is high. The resolution is better than 0.01% FS. This is an accuracy that is difficult to achieve with other sensors.
- Good safety: the magnetostrictive liquid level gauge has high explosion-proof performance. Safer to use. Especially suitable for the measurement of chemical raw materials and flammable liquids. It is not necessary to open the tank lid during measurement. There is no insecurity for manual measurement.
- Strong reliability: Because the magnetostrictive liquid level gauge uses the waveguide principle. There are no mechanically movable parts. So there is no friction and no wear. The entire converter is enclosed in a stainless steel tube and does not contact the measuring medium. The sensor works more reliably and has a longer life.
- Facilitate system automation: The secondary instrument of the magnetostrictive liquid level gauge adopts standard output signal. Help the computer to process the signal. It is easy to work on the Internet. Improve the automation of the entire measurement system.
- Simple installation and maintenance: the magnetostrictive liquid level gauge is usually installed through the existing nozzle on the tank top. It is especially suitable for the installation of underground storage tanks and already put into operation. And will not affect normal production during the installation process.
Extended reading: Types of Fuel-Diesel Level Sensors
What is tank level measurement
Tank level measurement is a general term for measuring the static storage of liquid products in large storage tanks. It can be used for inventory measurement, which is to determine the total amount of products in the storage tank.
It can also be used for transmission and transfer measurement, that is, as a basis for product purchase, sale and tax payment. There are two main methods: volume-based and mass-based measurement.
Tank level measurement devices
Extended reading: ultrasonic level sensor for diesel tank
Tank level measurement using pressure
Pressure level sensors can be used to establish levels in rivers, tanks, wells or other liquids. The pressure at the bottom of the liquid-filled container is directly related to the height of the liquid.
The transmitter measures this hydrostatic head and provides a final level. In order to obtain an accurate reading, the measuring device must be located at the lower point where you want to measure; it is usually installed or placed at the bottom of the container.
When measuring the liquid level, the specific gravity must be considered. Consider the following equation:
H = P / SG or P = SG? H
H-the height of the measured liquid. It is usually measured in inches, centimeters, meters, feet, etc.
P-Hydrostatic head at the bottom of the tank. Usually in inches of water column, feet of water column, horizontal bar, psi, Pascal’s, etc.
SG-the proportion of the medium. The dimensionless number is calculated from: measured medium density ÷ water density at 4 ° C. For example, the density of kerosene is equal to 0.82 g / cm 3. Therefore, the kerosene of SG is 0.82g / cm 3 · 1.00g / cm 3 = 0.82.
Extended reading: Radar Liquid Level Sensor|Corrosive, steam, volatile liquids
Radar tank level measurement
Radar level transmitter, also called Radar level gauge. Non-contact Continuous level measurement in liquids and solids with free space radar sensors. Non-contacting radar, based on microwave technology, detects only surfaces that reflect energy.
These transmitters work on the principle of a radar by using radio wave emissions. Mounted at the top of a tank filled with a liquid. The transmitter sends a radar signal into the liquid, and receives a reflection of the signal. The transmitters then analyze the current fill level of the tank based on the time taken by the transmitted signal to return.
Radar Level Sensor Features
- Non-contact, continuous level measurement over larger ranges
- Unaffected by sludge and biomass, dust, foam, oil, grease and other coatings, uneven surfaces, turbulence, pressure, and vacuum
- Single frequency radar level sensors for liquid sensing, dual frequency radar level sensors for level measurement of aggregates, gravel, sand, coal, asphalt, and other solids
- Simple mounting and push-button calibration
More about Radar level measurement
FAQ
How do you measure the depth of water in a tank?
The water level sensor of your water tank is an essential component. If not repaired or replaced, a sensor can become damaged over time and fail entirely. Too much water can cause a malfunction and too little water means inadequate water pressure. Either way, repairing or replacing holding tanks is an expensive task you shouldn’t have to undertake because of sub-par sensors.
With Sino-Inst’s water tank level sensors, there’s nothing to break down or rust and our models have a 99% success rate!
In the high unlikely event that you experience any issues with your product, call us and we’ll replace or repair it immediately at no charge.
How do I test my water level?
Water pressure transducers also called a water pressure sensor,
are pressure transmitters that can measure water pipe pressure.
For the water level/water depth measurement,
in the tank, or in the well, we can use electrical transmitters,
stainless steel body, IP65-IP6, 4-20ma output.
Sino-Instrument offers over 10 level transmitters for tank level measurement. About 50% of these are liquid level meters, 40% is the tank level sensor.
A wide variety of level meters options are available to you, such as free samples, paid samples.
Sino-Instrument is a globally recognized supplier and manufacturer of level measurement instrumentation, located in China.
Request a Quote
Wu Peng, born in 1980, is a highly respected and accomplished male engineer with extensive experience in the field of automation. With over 20 years of industry experience, Wu has made significant contributions to both academia and engineering projects.
Throughout his career, Wu Peng has participated in numerous national and international engineering projects. Some of his most notable projects include the development of an intelligent control system for oil refineries, the design of a cutting-edge distributed control system for petrochemical plants, and the optimization of control algorithms for natural gas pipelines.