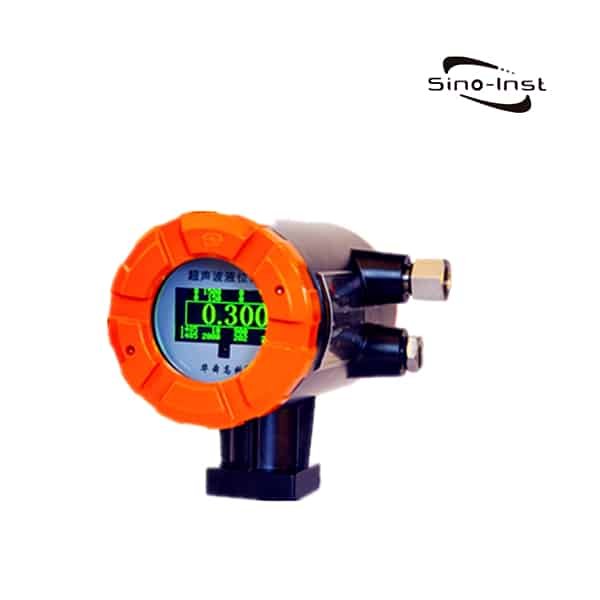
The HS-2000 External Ultrasonic Tank Level Sensor is a Non-invasive/non-contact device that accurately measures liquid levels in sealed tanks. To measure the liquid level in the tank by sticking an external sensor to the bottom of the tank. Its advanced technology and easy installation make it ideal for various liquids, including toxic or acidic ones.
Sino-Inst offers a variety of Ultrasonic Tank Level Sensors for industrial tank level measurement. If you have any questions, please contact our sales engineers.
External ultrasonic tank level sensor
HS-2000 External Mounted Ultrasonic Tank Level Sensor- (referred to as “external level gauge”). It adopts advanced signal processing technology and a high-speed signal processing chip. It breaks through the influence of container wall thickness. Realizes the height of the liquid level in the closed container True non-contact measurement.
The ultrasonic liquid level sensor (probe) is installed directly under the outer wall (bottom) of the container under test. Calibrate the outer wall of the probe. There is no need to open holes for the container to be tested, easy to install, and does not affect production.
It can accurately measure the level of various toxic substances, strong acids, strong alkalis, and various pure liquids in high-pressure airtight containers.
The HS-2000 External Mounted Ultrasonic Tank Level Sensor has no special requirements for the material of the liquid medium and the container. The explosion-proof design is adopted to meet the explosion-proof requirements.
Features of HS-2000 Ultrasonic Tank Level Sensor
- Non-contact measurement function ——– Ultrasonic sensor probe is external. No need to open a hole in the container to be tested.
- Auto-calibration function——–With self-calibration function. It overcomes the problem of reduced accuracy after the long-term use of traditional liquid level gauges.
- Infrared online debugging function——–Applicable to occasions where it is not suitable to open the cover for testing in dangerous situations. At the same time, it reduces the difficulty of debugging.
- Self-diagnosis function——–It has its own working status diagnosis function. It also has a hardware diagnosis function. It enhances the reliability and stability of the level gauge.
- One-key recovery function——–When the external measuring level gauge works abnormally, it can be restored to the normal state with one key through the debugger.
- Local display and remote transmission function——–The level gauge can not only display the level value on the spot in time. But also remotely transmit it to the control room through the signal line.
Specifications of HS-2000 Ultrasonic Tank Level Sensor-External Mounted
Measuring range | 3m, 5m, 10m, 20m, 30m |
Display resolution | 1mm |
Short time repetition | 1mm |
Measurement error | ±1‰FS (Excessive wall thickness and temperature/pressure instability may affect measurement precision.) |
Span shift | ±10 m |
Current output | 4~20mA,Max load 750Ω |
Communication interface | RS-485, IrDA |
Operating ambient temperature for liquid level meter | -30℃~+70℃ |
Operating ambient temperature for ultrasonic probe | -50℃~+100℃ (Probes with a wider temperature range can be provided upon request) |
Operating ambient humidity | 15%~100%RH |
Explosion proof mark | Ex d ⅡC T6 Gb |
Housing ingress protection | IP 67 |
Volume percentage display | 4-digit OLED display |
Blind area | There is a small blind area for the liquid level meter that should be noted |
Mediums that Ultrasonic Tank Level Sensor can measure
Liquefied Gas | Liquid Ammonia | Dimethyl ether | Liquid Chlorine | Hydrochloric Acid |
Propylene | Aqua Carbolisata | Lacquer Thinner | MTBE | Dimethylhydrazine |
Nmethyl anilineju | Butadiene | Chlorethylene | Light Hydrocarbon | Bromine |
Anhydrous Hydrogen Fluoride | Toluene | Methylamine | Gasoline | C3 |
Liquefied Carbon dioxide | Xylol | Carbon Dichloride | Epoxyethane | Acetone |
Plant Oil | Ethanol | Freon | Diethyl Ether | Diesel |
Ethylene | Sulfuric Acid | Methanol | Kerosene | Nitric Acid |
And More…….. |
Ultrasonic Tank Level Sensor’s Application
- Petrochemical industry
- Chemical industry
- Foodstuffs
- Pharmaceutical industry
- Marine industry
- Oil refining industry
- Refrigeration industry
Extended reading: Fuel-Diesel-Water Tank Level Sensor Monitoring
Chemical industry.
Common medium: liquid ammonia,liquid chlorine, hydrochloric acid, bromine,
chlorethylene,sulfuric acid, freon, and nitirc acid.
Coal chemical industry
Common medium: freon,liquid ammonia, butadiene, H2S.
Petrochemical industry.
Common medium : liquefied gas, propylene, ethylene, butadiene, light hydrocarbon, C3.
Power, food, pharmaceutical industries and so on.
Extended reading: Radar Oil Tank Level Sensor
In addition to measuring tank level, we also provide Portable Ultrasonic Water Depth Gauge for water depth measurement.
External Ultrasonic Tank Level Sensor Working Principle
The External Ultrasonic Tank Level Sensor adopts the sonar echo ranging principle. It overcomes the influence of the tank wall on the transmission of ultrasonic signals. It adopts advanced digital signal processing technology. It can truly realize non-contact, high-precision measurement of the liquid level in the tank.
The External Ultrasonic Tank Level Sensor can output 4-20mA standard signals or output the measurement results to the upper computer (or secondary meter) through the RS-485 interface. It can meet the automatic control of the system.
Extended reading: The Secret of Ultrasonic Level Measurement
Application Requirement
1.Medium’s Purity Degree
Liquids should not contain dense foam
There should be minimal suspended objects in the liquid, such as crystallized particles, etc.
There should be minimal precipitation in the tank, such as mud, sand, etc.
2.Tank Material:Carbon steel, stainless steel. Various hard metals. Glass fiber-reinforced plastics. Epikote, rigid plastics, ceramics. Glass, ebonite. Other composite materials.
3.Tank Shape:Spherical, horizontal and vertical tanks are permitted.
If you need to measure river water level, open channel level, etc. The Ultrasonic Liquid Level Sensor can be used for non-contact continuous level monitoring.
Read more about: Top 5 Ultrasonic Level Sensor Applications
How to Choose an Ultrasonic Tank Level Sensor?
To choose a suitable Ultrasonic Tank Level Sensor, users need to understand their measurement conditions and needs.
- Are you measuring a liquid or bulk material?
- What is the size of the tank? What level measurement range do you need?
- Is the location classified as a Hazardous Location or Explosive Atmosphere?
- Point level or continuous measurement?
- Will the material coat or buildup on surfaces?
- Does turbulence, foam, or vapor occur at the surface of the liquid?
- What kind of output will you need?
- Installation location and installation size?
Extended reading: Guide to Ultrasonic Level Transmitters
Ultrasonic tank level bottom sensor
The ultrasonic sensor (probe) is installed at the bottom of the tank’s external surface without the need for drilled holes in the tank. This allows for quick, simple installation that does not interrupt the tank’s operation.
External Ultrasonic Tank Level Sensor Installation
Featured Tank Level Sensors
FAQ
More Level Measurement Solutions
Sino-Inst offers over 10 Ultrasonic Tank Level Sensors for level measurement. About 50% of these are fuel level meters, 40% is the tank level sensor.
A wide variety of Ultrasonic Tank Level Sensor for level measurement options are available to you, such as free samples, paid samples.
Sino-Inst is a globally recognized supplier and manufacturer of Ultrasonic Tank Level measurement instrumentation, located in China.
Request a Quote
Wu Peng, born in 1980, is a highly respected and accomplished male engineer with extensive experience in the field of automation. With over 20 years of industry experience, Wu has made significant contributions to both academia and engineering projects.
Throughout his career, Wu Peng has participated in numerous national and international engineering projects. Some of his most notable projects include the development of an intelligent control system for oil refineries, the design of a cutting-edge distributed control system for petrochemical plants, and the optimization of control algorithms for natural gas pipelines.