Ultrasonic tank level sensors have become a popular choice for tank level monitoring due to their non-contact measurement, high accuracy, and easy installation. These sensors use high-frequency sound waves to measure the distance between the sensor and the surface of the liquid in the tank, and the time it takes for the sound waves to travel to the liquid surface and back is used to calculate the level.
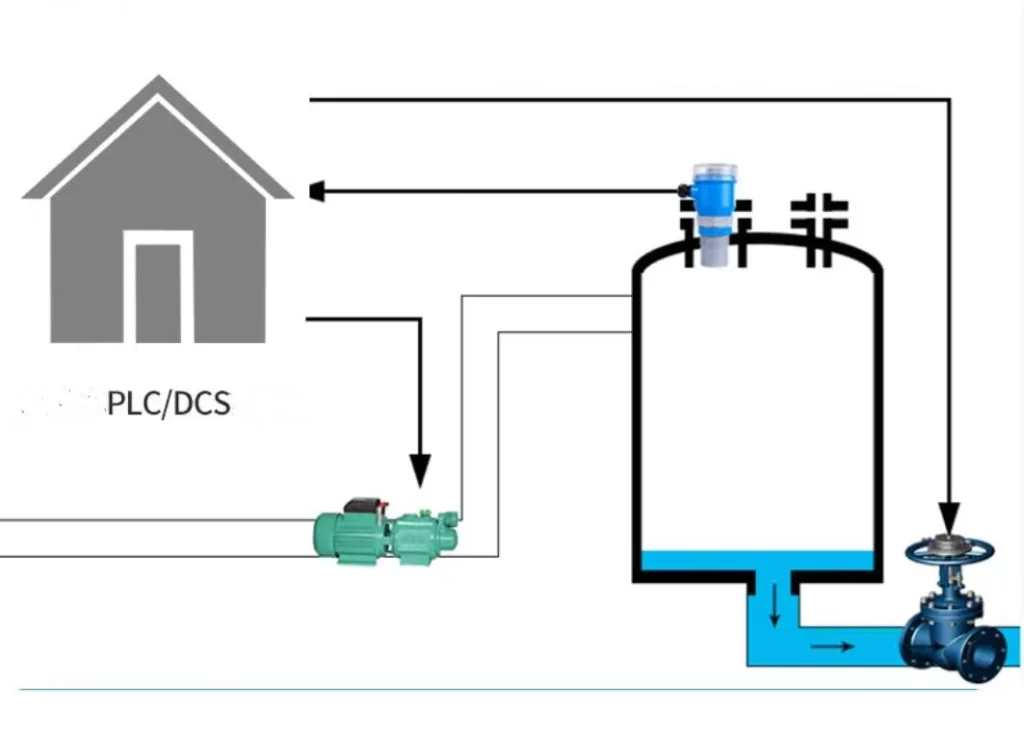
Top Ultrasonic Tank Level Sensors
Tank Level Monitoring
Tank level monitoring is an essential aspect of managing liquid storage and ensuring efficient operations across various industries. There are several methods and technologies available to achieve accurate and reliable tank level monitoring. Here, we will outline the general steps and factors to consider when implementing a tank level monitoring system:
Choose the right level measurement technology: Several technologies can be used for tank level monitoring, including ultrasonic, radar, capacitive, and hydrostatic. Each technology has its advantages and disadvantages, depending on the type of liquid, tank size, and environmental conditions. It’s crucial to choose the appropriate technology that best suits your specific application.
Select the appropriate level sensor: Once you’ve determined the most suitable measurement technology, it’s essential to choose a level sensor that meets your specific requirements. Consider factors such as range, accuracy, resolution, and compatibility with the liquid being measured. You may also need to consider certifications and ratings for hazardous environments if applicable.
Install the level sensor correctly: Proper installation of the level sensor is critical for accurate and reliable measurements. Ensure that the sensor is mounted at the correct location and angle, free from obstructions and interferences that could affect the sensor’s performance. Follow the manufacturer’s guidelines and best practices for installation.
Integrate the sensor with a control system: To make the most of your tank level monitoring system, it’s essential to integrate the sensor with a control system that can display real-time data, generate alerts, and automate processes. This can be done using programmable logic controllers (PLCs), human-machine interfaces (HMIs), or dedicated tank level controllers.
Establish a data communication network: A robust data communication network is necessary for transmitting sensor data to the control system and other devices. You can choose from wired or wireless communication options, depending on your infrastructure and connectivity requirements.
Perform regular maintenance and calibration: To ensure the ongoing accuracy and reliability of your tank level monitoring system, it’s important to perform regular maintenance and calibration. This includes cleaning the sensor, checking for wear and damage, and calibrating the sensor according to the manufacturer’s recommendations.
Analyze and optimize: Monitor the performance of your tank level monitoring system and use the data collected to identify areas for improvement and optimization. This can help you enhance the efficiency of your operations, reduce costs, and prevent potential issues before they become critical.
By following these steps and carefully considering the factors involved, you can successfully implement a tank level monitoring system that meets your specific needs and provides accurate, reliable data to optimize your operations.
Read more about: Ultrasonic Level Sensors for Liquids Applications
Monitors Liquid Volume Solutions
Ideally, we should be able to use a liquid volume sensor to directly measure the volume of the liquid in the container. Well, but in fact, there is no mature liquid volume sensor product on the market.
Because there are various shapes of liquid containers. Such as cylinders, spheres, rectangles, cylinders and squares with hemispherical ends.
So why are we talking about liquid volume sensor here? Don’t worry, we don’t have a mature liquid volume sensor. However, we have A dozen ways for liquid level measurement, with different level sensors. Combined with Sino-Inst’s volume recorder. It can collect, display and convert the liquid level of various regular and irregular tanks in the industrial field into the corresponding tank volume. It is suitable for monitoring, controlling and collecting various process parameters.
Read more about Monitoring liquid volume solutions.
More Tank Level Measurement Solutions
New Choice for Heating Oil Tank Level Sensor
Ship Ballast Tank Pressure-Liquid Level Measurement
Fuel Tank Diesel Level Sensors
Ultrasonic Level Sensor for Diesel Tanks | 5~150cm,0-30m
Cryogenic Level Sensor for Liquid Nitrogen Tank Level Indicator
External Tank Level Indicator
Ultrasonic tank level sensors have proven to be a reliable, accurate, and efficient solution for tank level monitoring across various industries. By understanding their working principles, advantages, and applications, you can make an informed decision and choose the best ultrasonic tank level sensor for your specific needs.
At Sino-Inst, we are experienced manufacturers and suppliers of ultrasonic tank level sensors, offering customized solutions to meet your unique requirements. If you have any questions or need assistance in selecting the right sensor, feel free to contact us. Let us help you revolutionize your tank level monitoring and optimize your business operations.
Explore our range of ultrasonic tank level sensors and find the perfect solution for your needs. Contact us today!
Request a Quote
Wu Peng, born in 1980, is a highly respected and accomplished male engineer with extensive experience in the field of automation. With over 20 years of industry experience, Wu has made significant contributions to both academia and engineering projects.
Throughout his career, Wu Peng has participated in numerous national and international engineering projects. Some of his most notable projects include the development of an intelligent control system for oil refineries, the design of a cutting-edge distributed control system for petrochemical plants, and the optimization of control algorithms for natural gas pipelines.