Pressure Transmitter 4-20mA is the most commonly used one in industrial process control. In industrial process control, the measurement and control of pressure has always been a very important parameter. The 4-20mA output pressure transmitter is widely used due to its own characteristics, such as: good anti-interference performance, less and simple wiring, etc.
Sino-Inst sorted out the corresponding solutions according to the problems that customers often encountered in the process of installing and using this type of pressure transmitter. In particular, it pointed out that this article is aimed at common problems in the use of 4-20mA output pressure transmitters.
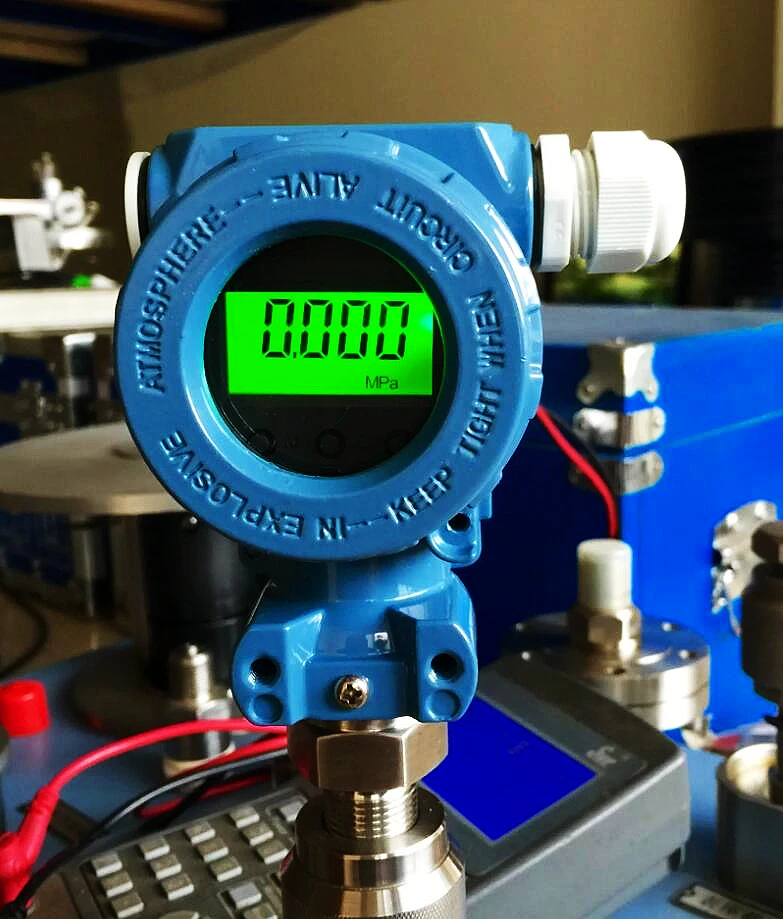
Featured 4-20ma Pressure Transmitters for Sale
Troubleshooting for 4-20ma Pressure Transmitter
1. The pressure transmitter has no output and no display
Extended Reading: Resistive Pressure Transducer
2. Pressure transmitter output ≥ 20mA
3. Transmitter output≤4mA
4. The pressure display/output signal is incorrect and has errors
Extended Reading: Smart pressure transmitter
5. The pressure control system cannot be connected
The input of the pressure indicating instrument is 4~20mA, and the output signal of the transmitter can be directly connected.
If the input of the pressure indicating instrument is 1~5V. Then a resistor with a precision of 1/1000 or above and a resistance of 250Ω must be connected to the input terminal of the pressure indicating instrument. Then connect to the input of the transmitter.
No matter which pressure transmitter you choose. The signal output by the pressure transmitter, such as 4-20mA. The pressure signal can be interfaced to a paperless recorder. Multi-channel pressure signal monitoring.
6. recorder no record
When the multipoint paper recorder does not record. If the input is open, then:
- No other loads can be carried;
- Use another recorder with input impedance ≤250Ω when there is no record.
7. The temperature of the pipeline is too high
The temperature of the pipeline is too high, add a buffer tube to dissipate heat. It is best to add some cold water to the buffer tube before use. In order to prevent the superheated steam from directly impacting the sensor. Thereby damaging the sensor or reducing the service life.
Read more about: Pressure Sensor Applications-Featured Industry Applications
8. Pressure Transmitter 4-20mA installation problem
In steam flow measurement, steam mainly involves two kinds, one is external steam, and the other is superheated steam of boiler.
The externally supplied steam is the steam after decompression and decompression. The temperature is not high, and it is mixed with a lot of water. It needs to be used and not used. The steam flow rate can be changed according to the user’s requirements.
In the actual flow measurement process, sometimes the flow rate is too large and sometimes the flow rate is too small. It is very unstable. Blowdown is often required. The measurement of the transmitter is accurate after each blowdown. All joints on the pressure guiding pipe leak steam.
In the use of measuring superheated steam, the biggest problem found is that sometimes the machine shuts down, and the flow rate will deviate after restarting, resulting in inaccuracy. Sometimes there is still a little flow display after stopping.
Generally, the installation position of the transmitter is lower than the measuring pipe. But in the actual installation, the condensing tank and the transmitter for external steam flow are both higher than the measuring pipe, and the pressure guiding pipe that is laid down at least 1 meter from the throttling device is too short.
The superheated steam flow of the boiler also has the problem of inconsistent heights between the condensing tank and the measuring pipe. This leads to an imbalance in the height of the condensed water, which causes a static pressure difference.
9. Pressure guide pipe blockage problem
In pressure measurement, sometimes the indicated pressure does not vary with operating conditions. After opening the drain valve, there is only a small amount of sewage and no water flows out. This is because there will be a small amount of floating dust in the water quality or compressed air, which will enter the pressure guiding pipe for sedimentation along with the water flow. After a long period of operation, the wall of the pressure guiding pipe will be corroded and fouled, and blockage will occur.
10. Pressure Transmitter 4-20mA equipment itself fault problem
In the measurement of lubricating oil pressure, since the lubricating oil pressure signal participates in the shutdown interlock control. The signal measured by the lubricating oil pressure transmitter is transmitted to the computer. On the one hand, it is displayed. On the other hand, the signal is compared by the program. When the pressure is lower than 0.06MPa, it will send a signal to stop due to lack of oil.
From the trend graph of the lubricating oil pressure signal, it can be seen that the pressure is an instantaneous drop in a straight line, resulting in a trip. After checking the transmitter, it was found that the internal module of the transmitter was damaged. Although the transmitter is regularly calibrated every year, it is used for production after passing the test.
After several years of operation of the transmitter, its accuracy, sensitivity, stability and other performance indicators will gradually decrease. The internal diaphragm and integrated block will also be damaged and malfunction.
11. There is an interference problem
In the measurement of the exhaust pressure of the air compressor, the fluctuation of the exhaust pressure signal is large. After the transmitter is verified, it meets the accuracy requirements, and the fault of the transmitter itself is eliminated.
Check that the pressure guide tube and connector are not damaged or leaked. The connection of the signal cable is in good contact.
However, the direction of the cables is introduced into the control room through the cable bridge next to the high-end distribution room. There is a lot of electromagnetic interference around.
Learn More About Pressure Transmitter 4-20mA
If you cannot find an answer to your question in our Pressure Transmitter 4-20m, you can always contact us and we will be with you shortly.
More Pressure Measurement Solutions
Sino-Inst is a manufacturer of Pressure Transmitter 4-20mA. We offer more than 50 types of Transmitters. Main products include compact pressure transmitters, industrial pressure transmitters, differential pressure transmitters, single crystal silicon pressure transmitters, diffused silicon pressure transmitters , Diaphragm pressure transmitter, high temperature pressure transmitter, explosion-proof pressure transmitter, pressure transmitter, custom pressure transmitter, with remote pressure transmitter, 316 diaphragm pressure transmitter.
The Pressure Transmitter 4-20mA is mainly used to measure the pressure and liquid level of the medium. In industrial production, it is widely used. Sino-Inst pressure transmitter adopts high-quality diffused silicon type, and the pressure transmitter adopts a dedicated integrated module. Fine temperature, zero point, full scale and nonlinear compensation. Realize accurate measurement and transmission of pressure changes in liquid, gas, steam and other media. Realize the ideal monitoring of changes in pressure and vacuum media in various places for enterprises, scientific research institutes and other departments.
Sino-Inst’s Pressure Transmitters 4-20mA are the most commonly used sensors in industrial applications. Widely used in water conservancy and hydropower, railway transportation, intelligent building, production control, aerospace, military industry, petrochemical industry, oil well, electric power, ship, machine tool, pipeline and other industries.
Sino-Inst’s entire team is well trained, so we can ensure that each customer’s needs are met. If you need any help with your product requirements, whether it is a Pressure Transmitter 4-20mA, level sensors, or other equipment, please give us a call.
Request a Quote
Wu Peng, born in 1980, is a highly respected and accomplished male engineer with extensive experience in the field of automation. With over 20 years of industry experience, Wu has made significant contributions to both academia and engineering projects.
Throughout his career, Wu Peng has participated in numerous national and international engineering projects. Some of his most notable projects include the development of an intelligent control system for oil refineries, the design of a cutting-edge distributed control system for petrochemical plants, and the optimization of control algorithms for natural gas pipelines.