In modern air conditioning and refrigeration systems, Pressure Transducers play a vital role. These precision devices not only monitor pressure changes in the system in real time, but also ensure the efficient and safe operation of the entire system. Accurate pressure monitoring is critical to maintaining optimal system performance and avoiding potential failures. Sino-Inst offers a range of pressure sensors optimized for air conditioning and refrigeration applications. Next, we will delve into the application of Pressure Transducers in air conditioning and refrigeration systems.
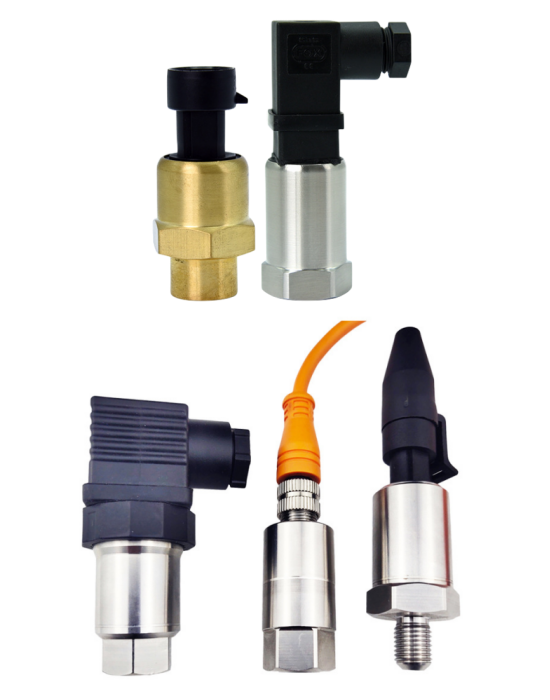
The necessity of pressure sensors in refrigeration
About Refrigeration cycle
To gain a deeper understanding of the role of refrigerants in the refrigeration process and its impact on pressure sensor requirements, we can analyze each step of the refrigeration cycle and its thermodynamic principles in detail:
Compression Phase: The refrigeration cycle begins with the compressor, where low-pressure refrigerant gas is compressed. During this process, the temperature and pressure of the refrigerant increase significantly. As the gas is compressed, the distance between the molecules decreases, resulting in an increase in energy, which increases the temperature.
Condensation stage: The high-temperature and high-pressure gaseous refrigerant then flows into the condenser. Here, it releases heat to the external environment, thereby condensing into a liquid state. This stage is a critical link in the transfer of heat from the refrigeration system to the external environment.
Expansion stage: The condensed liquid refrigerant passes through the expansion valve, and its pressure and temperature decrease significantly. During this process, the refrigerant partially evaporates, forming a low-temperature mixture of liquid and gas.
Evaporation stage: This low-temperature refrigerant mixture enters the evaporator, where it absorbs heat from the surrounding air and becomes gaseous again. This process causes the temperature of the surrounding environment to decrease, achieving a cooling effect.
The entire refrigeration cycle is a precise thermodynamic process, which has strict requirements on the pressure and temperature control of the refrigerant. Therefore, high-quality pressure sensors play a vital role in this process. They ensure that the refrigerant is maintained at optimal pressure and temperature at each stage to ensure efficient and stable operation of the entire refrigeration system.
So why should you care about measuring pressure in this whole process?
Benefits of pressure sensors in refrigeration
If your refrigeration system does not properly measure all inputs and outputs, your system will not operate properly. Typically, the pressure sensor is placed near the compressor outlet, but there can be more sensors depending on the application and complexity of the refrigeration system. The data collected by the pressure sensor is sent to the controller, which can automatically control the compressor in the system.
The following are the benefits of using pressure transmitters in air conditioning and refrigeration systems:
- Accurately monitor pressure: The pressure transmitter can accurately monitor the pressure within the system to ensure that the system is operating at its best.
- Improved cooling efficiency: Proper pressure levels help improve the cooling efficiency of the system while reducing energy consumption.
- Detect potential problems in time: Real-time monitoring can detect problems such as leaks or pressure abnormalities in time to prevent system failure.
- Reduce repair costs: By preventing failures, pressure transmitters help reduce repair costs and downtime.
- Extended system life: Reduces wear and damage caused by pressure fluctuations, extending the life of your air conditioning and refrigeration systems.
- Improve overall performance: ensuring efficient, reliable and economical operation of the entire air conditioning and refrigeration system.
How to Choose Pressure Transducers for Refrigerant
There are several key factors to consider when selecting and using pressure transmitters in different types of refrigeration systems:
Type and size of system: The first thing to consider is the type and size of the refrigeration system (such as a household air conditioner, commercial cold storage, or industrial refrigeration system). Different types and sizes of systems have different requirements for the accuracy and durability of pressure transmitters.
Temperature tolerance: The operating temperatures of refrigeration systems can be extremely different. Therefore, the pressure transmitter selected must be able to work properly within these temperature ranges to ensure accurate and stable performance.
Pressure range and accuracy: Different refrigeration systems may need to operate within different pressure ranges. When selecting a pressure transmitter, make sure it can provide accurate measurements over the required pressure range.
Ease of installation and maintenance: Choosing a pressure transmitter that is easy to install and maintain can reduce system downtime and maintenance costs.
In summary, when selecting and using a pressure transmitter, decisions should be made based on the specific refrigeration system type, operating environment, required pressure range and accuracy, and ease of installation and maintenance. This not only ensures efficient operation of the refrigeration system, but also improves overall safety and reliability.
Featured Refrigeration Pressure Transducers
Low pressure transducers for air and non-corrosive gases low pressure measurement. 0 ~ 2.5kPa to 0 ~ 30kPa measurable.
The 4-20mA/ Voltage Pressure Transducer,
also called pressure transmitter 4-20mA,
is a pressure sensor with4-20ma/Voltage output.
Digital Pressure Sensor is particularly suitable for use in computer control systems. RS485 half-duplex working mode.
Gas pressure sensor for industrial gas pressure monitoring. Pagoda gas nozzle Φ8. Such sensors are also commonly referred to as wind pressure transmitters, exhaust pressure sensors.
High pressure sensor is pressure transmitter designed for high pressure measure&control. 0 ~ 40MPa… 600MPa. M20 × 1.5, G1 / 2 (others are customized according to requirements)
Ceramic pressure sensor is a pressure sensor refined from a thick ceramic base using a refined ceramic base. Cost-effective. Support OEM processing. 0-0.2MPa -…- 40MPa
Combined pressure and temperature sensor for Simultaneous measurement of pressure and temperature.
Thermocouple types: J, K, E type or PT100 platinum resistance. Two outputs do not affect each other.
High Temperature Pressure Sensor for pressure measurement of high temperature gas or liquid. Such as steam pressure. High temperature up to 800 ℃.
More Pressure Measurement Solutions
- Analog Pressure Transducers vs Digital Pressure Transducers | How to Choose?
- Vacuum Pressure Transducers | Product List and FAQs
- What Is Psi in Pressure Sensor?
- What Is a Hydraulic Pressure Transducer? and Product List
- Pressure Transmitter Installation Guide
- What Is Pressure Transducer Output Signal? and Types
- Optimize Filtration Monitoring with Differential Pressure Sensors
- Low Cost Differential Pressure Sensor – Solve Big Problems!
- Oxygen Cleaning Pressure Sensor – No Oil, No Corrosion, No Impurities
- Voltage Pressure Transducer Comparison
- What Is a Differential Pressure Sensor?
- Top Digital Pressure Transducers with Display
- Why Shielded Twisted Pair Cables for Industrial Instrumentation
- Custom Case: Pressure Transducer Connector with 6 Pin Bendix Connector
Before deciding which pressure sensor your system will use, carefully define the needs of your refrigeration system. This will guide product selection and enable your team to create the most efficient refrigeration system possible.
Choosing a Sino-Inst pressure transmitter means choosing high accuracy, reliability and excellent customer service. Sino-Inst provides comprehensive customer support, including technical consultation, installation guidance and after-sales service, ensuring customers can make full use of our products.
Customer reviews and feedback are the best proof of our product quality and service. Many customers appreciate the performance and reliability of our pressure transmitters, especially in improving system efficiency and reducing maintenance costs. They also speak highly of our responsive customer service team, which not only strengthens their trust in our products but also enhances their experience.
In short, when you choose Sino-Inst’s pressure transmitter, you will get high-performance products and a first-class customer experience. We are committed to providing the best solutions for your refrigeration system needs.
Request a Quote
Wu Peng, born in 1980, is a highly respected and accomplished male engineer with extensive experience in the field of automation. With over 20 years of industry experience, Wu has made significant contributions to both academia and engineering projects.
Throughout his career, Wu Peng has participated in numerous national and international engineering projects. Some of his most notable projects include the development of an intelligent control system for oil refineries, the design of a cutting-edge distributed control system for petrochemical plants, and the optimization of control algorithms for natural gas pipelines.