Measuring Steam Flow
Measuring Steam Flow is a difficult task. But again, it’s a very important thing. Steam flow measurement is difficult, the main reason is determined by the characteristics of steam. Steam is a relatively special medium. With the change of working conditions (such as temperature, pressure). Superheated steam is often transformed into saturated steam, forming a vapor-liquid two-phase flow medium.
Steam is an important energy substance. For energy consumption calculation or cost accounting. An accurate metering of the steam consumed is usually required using a flow meter.
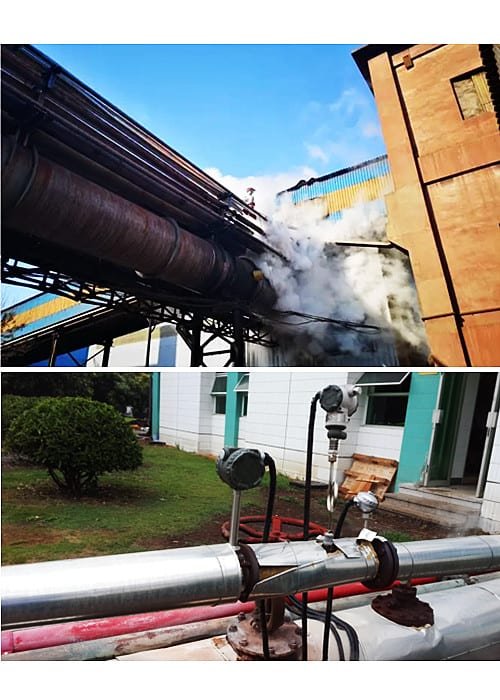
Steam Flow Meters for Sale
Inaccurate steam flow measurement is a common Requirement in the heating industry. The main reasons are as follows:
superheated steam
Steam is a relatively special medium. Generally speaking, steam refers to superheated steam. Superheated steam is a common power source. It is often used to drive steam turbines to rotate. And then drive the generator or centrifugal compressor to work.
Superheated steam is obtained by heating saturated steam. There is absolutely no droplet or liquid mist in it, and it is an actual gas.
The temperature and pressure parameters of superheated steam are two independent parameters. Its density should be determined by these two parameters.
After the superheated steam is transported over a long distance, it changes with the working conditions (such as temperature and pressure). Especially when the degree of superheat is not high, it will enter the saturated or supersaturated state from the superheated state due to the decrease of the heat loss temperature.
Converted to saturated steam or supersaturated steam with water droplets. The saturated steam is suddenly decompressed greatly. When a liquid expands adiabatically, it also turns into superheated steam. In this way, a vapor-liquid two-phase flow medium is formed.
Read more about: Condensate Flow Meter-Steam Condensate Flow Meter|Types & Selection Guide
Saturated Vapor
Steam that has not been heat treated is called saturated steam. It is colorless and odorless. Non-flammable and non-corrosive gases. Saturated steam has the following characteristics:
(1) There is a one-to-one correspondence between the temperature and pressure of saturated steam. There is only one independent variable between the two.
(2) Saturated steam is easy to condense. If there is heat loss during transmission. Droplets or mist form in the steam. and lead to a decrease in temperature and pressure. Steam containing liquid droplets or mist is called wet steam.
Strictly speaking, saturated steam contains more or less a two-phase fluid of liquid droplets or mist. Therefore, different states cannot be described by the same gas state equation.
The content of liquid droplets or mist in saturated steam reflects the quality of the steam. It is generally expressed by the parameter of dryness. The dryness of steam refers to the percentage of dry steam per unit volume of saturated steam. Indicated by “x”.
(3) It is difficult to accurately measure the flow rate of saturated steam. Because the dryness of saturated steam is difficult to guarantee. General flowmeters cannot accurately detect the flow rate of two-phase fluid. Fluctuations in steam pressure will cause changes in steam density. Additional errors will occur in the indication value of the flowmeter. .So in steam measurement, it is necessary to try to maintain the dryness of the steam at the measurement point to meet the requirements. If necessary, compensation measures should be taken to achieve accurate measurement.
Extended reading: What Is Difference Between Rotameter And Flow Meter?
Analysis of Steam Measurements
Flow meters are currently used to measure steam flow. The measurement medium refers to single-phase superheated steam or saturated steam.
For steam with frequently changing phase flow, there will definitely be inaccurate measurements.
The solution to this problem is to keep the steam superheated and minimize the water content of the steam.
For example, strengthen the insulation measures of steam pipelines and reduce the pressure loss of steam. to improve the measurement accuracy.
However, these methods cannot completely solve the problem of inaccurate steam flow measurement. The fundamental solution to this problem is to develop a flow meter that can measure two-phase flowing media.
There are many types of flow meters used to detect gas flow. The most common applications are velocity and volumetric flow meters. Their common feature is that they can only measure the volume flow under operating conditions continuously. The volume flow is again a function of the state.
The volume flow in the working state cannot exactly represent the actual flow.
In engineering, it is generally expressed as standard state volume flow or mass flow.
The so-called standard state volume is the volume of gas at 0°C and 1 standard atmosphere or the volume at 20°C and 1 standard atmosphere.
The case where mass flow is the unit of measurement. At present, when the scale gas flow meter is not used in many applications. The normal temperature and pressure of the selected gas are the design conditions. Convert the volume flow under the design state to standard volume flow or mass flow. Its conversion coefficient contains the factor of gas density. When the working state of the gas medium deviates from the design state, the flow indication value will have errors.
Furthermore the composition, content or temperature of the gaseous medium changes. It also affects flow measurement. Therefore, the measurement of steam flow needs to take compensation measures. In addition, the compensation factors due to the state change of the steam are also complicated.
The density of superheated steam is determined by the temperature and pressure of the steam.
And in different ranges of parameters, the expression of density is also different. cannot be represented by the same general formula. Therefore, a unified density calculation formula cannot be obtained.
The temperature and pressure compensation formulas can only be derived individually.
In the case of large temperature and pressure fluctuation range. Except for temperature and pressure compensation. Compensation for the gas expansion coefficient Σ also needs to be considered.
No matter what kind of flow meter is used to detect the flow of saturated steam. When working under conditions of steam pressure fluctuations, pressure compensation measures must be taken. This is because the steam density factor is included in the flow equation. When the operating conditions are inconsistent with the design conditions, the readings will have errors. The size of the error and the working pressure are related to the size of the design pressure deviation. A negative error will occur if P real > P set. Otherwise there will be a positive error.
The dryness condition of steam is an important condition related to whether the steam flow can be accurately measured. At present, the online steam dryness testing instrument is being developed. The application of the dryness meter to the steam flow measurement and compensation system will further improve the measurement accuracy. The following three measures should be taken at present:
- The pipeline for conveying steam must have good insulation measures to prevent heat loss.
- Drain the steam pipeline section by section, and set steam traps at the lowest part of the pipeline and the pipeline in front of the instrument to drain the condensed water in time.
- During the operation of the boiler, the phenomenon that the liquid level of the steam drum is too high should be avoided, and the large fluctuation of the load should be minimized.
Selection of Steam Flow Meters
There are 5 main factors to consider when choosing a flow meter for steam metering:
Characteristics of the fluid being measured, production process conditions, installation conditions, maintenance requirements, and characteristics of the flow meter.
Here, we focus on discussing the characteristics, installation conditions, maintenance requirements and several issues that should be paid attention to when choosing a flow meter.
At present, the instruments for measuring steam flow mainly include vortex flowmeter, differential pressure type (orifice plate, uniform velocity tube, elbow) flowmeter, split rotor flowmeter, Annubar flowmeter, float flowmeter, etc.
Frequently
Asked
Questions
Related Blogs
The choice of Measuring Steam Flow and steam flow meter is very important. Accurately measuring steam flow is a need and a common concern in the production sector. With the development of the economy, the voice of improving the measurement level is getting louder and louder.
We should choose the appropriate flowmeter according to the actual measurement conditions.
The choice of Measuring Steam Flow and Steam Flow Meters has always been an industry challenge.
Sino-Inst, Manufacuturer for Steam Flow Measurement Flowmeters.
Sino-Inst’s Steam Flow Measurement Flowmeters, made in China, Having good Quality, With better price. Our Steam Flow Measurement instruments are widely used in China, India, Pakistan, US, and other countries.
Request a Quote
Wu Peng, born in 1980, is a highly respected and accomplished male engineer with extensive experience in the field of automation. With over 20 years of industry experience, Wu has made significant contributions to both academia and engineering projects.
Throughout his career, Wu Peng has participated in numerous national and international engineering projects. Some of his most notable projects include the development of an intelligent control system for oil refineries, the design of a cutting-edge distributed control system for petrochemical plants, and the optimization of control algorithms for natural gas pipelines.