Liquid Ammonia Density might not be a term you come across in everyday conversation, yet its significance in modern industries is profound. From the refrigeration systems that keep our groceries fresh to the manufacturing processes that produce everyday items, the density of liquid ammonia plays a pivotal role. Accurate measurements of properties like ammonia’s density become essential.
In the following sections, we’ll explore the ins and outs of liquid ammonia, its properties, and the technological advancements making accurate density measurements more accessible than ever.
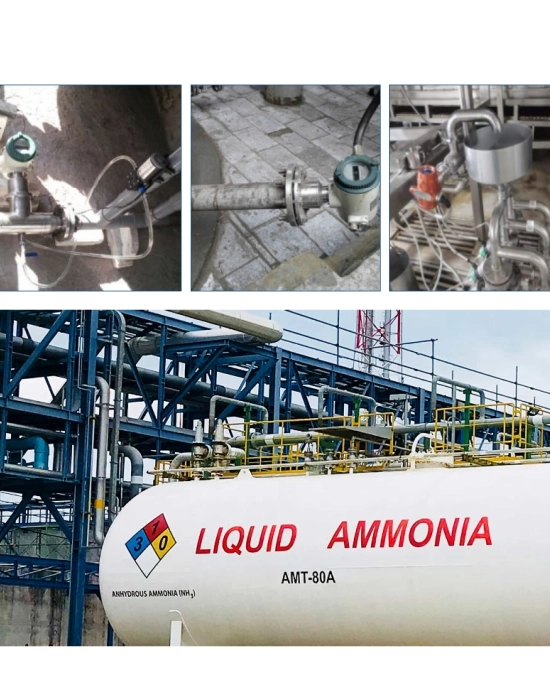
Featured Industrial Liquid Ammonia Density Meter for you
Whether you are new to the industry or an experienced measurement and control engineer, it is necessary to understand What is the density of liquid ammonia and related information.
Basic properties of Liquid Ammonia [NH3]
In wrapping up, liquid ammonia’s properties make it a cornerstone in various industrial applications. By understanding its basic traits, we gain insight into how and why it’s used, emphasizing the marvelous interplay between science and our daily lives.
Liquid Ammonia Density: Common Units Simplified
In the world of science and industry, measurements and units are crucial. They ensure consistency, safety, and efficiency. For liquid ammonia density, there are several units commonly used, each serving its purpose based on the context. Let’s decode these units in a simple and straightforward way.
- Kilogram per Cubic Meter (kg/m^3):
This is a standard unit to measure density. Think of it like this: Imagine a box that’s a meter wide, long, and tall. If you fill that box with liquid ammonia, the weight of that ammonia in kilograms represents its density in kg/m^3. For instance, at room temperature (25°C), liquid ammonia has a density of about 682 kg/m^3. - Pound per Cubic Foot (lb/ft^3):
This is another way to measure density but using pounds and cubic feet. It’s especially familiar in countries using the imperial system. For our liquid ammonia, its density is roughly 42.6 lb/ft^3 at room temperature. - Pound per US Gallon (lb/gal):
A gallon is a unit of volume often used for liquids, especially in the United States. So, when we measure how many pounds of liquid ammonia fit into one US gallon, we get a density of approximately 5.68 lb/gal at 25°C. - Gram per Milliliter (g/mL):
A milliliter is a tiny cube that’s a centimeter on each side. It’s a commonly used volume in the scientific world. At room temperature, liquid ammonia’s density is 0.682 g/mL. - Ounce per Cubic Inch (oz/in^3):
This unit is more specialized but can still be used for specific applications. It indicates the weight in ounces of liquid ammonia that would fit into a cube measuring one inch on all sides. For ammonia, this comes to about 0.394 oz/in^3 at 25°C.
Understanding the units of liquid ammonia density isn’t just about numbers and measurements. It’s about appreciating the consistency and standards that allow industries to function smoothly and safely. Each unit has its place and is selected based on the context and region, ensuring that everyone speaks the same “language” when it comes to measuring this vital substance.
Read More About: Density 101: What Is the Unit of Measurement for Density
Liquid Ammonia is Important for Industries
Liquid ammonia might seem like a mysterious substance to many of us, but it plays a silent yet powerful role in several industries we rely on every day. Let’s explore where this unique liquid truly makes its mark.
- Agriculture:
Farmers use liquid ammonia as a primary source of nitrogen in fertilizers. This nitrogen helps plants grow strong and healthy, leading to the fruits and vegetables we enjoy on our tables. - Refrigeration:
Ever wondered how our food stays cold in large warehouses or during transport? The answer often lies in refrigeration systems that use liquid ammonia. It’s efficient, effective, and helps keep our food fresh. - Pharmaceuticals:
When we’re feeling under the weather and reach for certain medications, we might be benefiting from liquid ammonia’s role. It’s a key component in the production of some medicines, ensuring they’re both safe and effective. - Cleaning Supplies:
Ammonia is also an active ingredient in many household cleaning agents. It helps cut grease, brighten surfaces, and ensure our homes and offices sparkle. - Textile Industry:
Our clothes go through many processes before they reach us. In the textile industry, liquid ammonia is used to treat cotton, making it stronger and giving it a soft, attractive finish. - Plastic Manufacturing:
Some of our everyday plastic items owe their existence to liquid ammonia. It’s a critical component in the production of certain plastics, ensuring they’re durable and fit for purpose.
Of course, density measurement of liquid ammonia is important. Similarly, liquid ammonia flow, temperature, pressure, and liquid level measurement are also important.
In addition to supplying liquid ammonia density meters, Sino-Inst also provides liquid ammonia flow meters, liquid ammonia temperature, liquid ammonia pressure transmitters, and liquid ammonia level meters.
More Featured Industrial Liquid Ammonia Measuring instruments
What Is Density Flow Meter: Principles and Applications
What Is the Density of Crude Oil and How to Measure?
Coriolis Flow Meter Density Measurement: Principles and Benefits
Industrial Online Dew Point Meters | Sino-Inst
Industrial Slurry Density Measurement-Featured Slurry Density Meters
Industrial Applications of Various Density Meters
Related Documents:
- Compound Summary: Liquid Ammonia. National Center for Biotechnology Information; U.S. National Library of Medicine; 8600 Rockville Pike; Bethesda, MD 20894 USA. Last accessed: 29 August 2020. Link.
- Ammonia Production and Uses. International Fertilizer Industry Association; Paris, France. Last accessed: 28 August 2020. Link.
- Ammonia Refrigeration Basics. International Institute of Ammonia Refrigeration (IIAR); Alexandria, VA, USA. Last accessed: 30 August 2020. Link.
In our journey through the intricacies of liquid ammonia density, we’ve uncovered the crucial role it plays in various sectors. Its importance in industries ranging from agriculture to refrigeration underscores the science’s impact on our daily lives. Yet, the world of measurement doesn’t stop at ammonia density.
Did you know that accurate measurements are equally crucial in other domains? At Sino-Inst, we dive deeper into the world of precision. From crude oil flow measurement ensuring efficient transportation of our primary energy source, level measurements which are vital for storage tanks and reservoirs, to temperature measurements ensuring that processes remain within desired ranges – we’ve got it all covered.
With a rich tapestry of experience, Sino-Inst stands proud as a leading manufacturer and supplier in the world of instrumentation. Whether you’re looking for standard instruments or need a customized solution, our team is here to guide and assist. Reach out to Sino-Inst today and elevate your measurement game!
Request a Quote
Wu Peng, born in 1980, is a highly respected and accomplished male engineer with extensive experience in the field of automation. With over 20 years of industry experience, Wu has made significant contributions to both academia and engineering projects.
Throughout his career, Wu Peng has participated in numerous national and international engineering projects. Some of his most notable projects include the development of an intelligent control system for oil refineries, the design of a cutting-edge distributed control system for petrochemical plants, and the optimization of control algorithms for natural gas pipelines.