Torque sensors are essential components in many mechanical systems. They measure the torque, or rotational force, applied to a rotating system such as a motor, crankshaft, gearbox, or capstan. In essence, the torque sensor is like the heartbeat monitor of a machine, providing critical performance data.
But let’s focus on one type in particular: the shaft torque sensor. These unique sensors directly measure the torque on a rotating shaft. Providing real-time, highly accurate measurements crucial for monitoring and control applications.
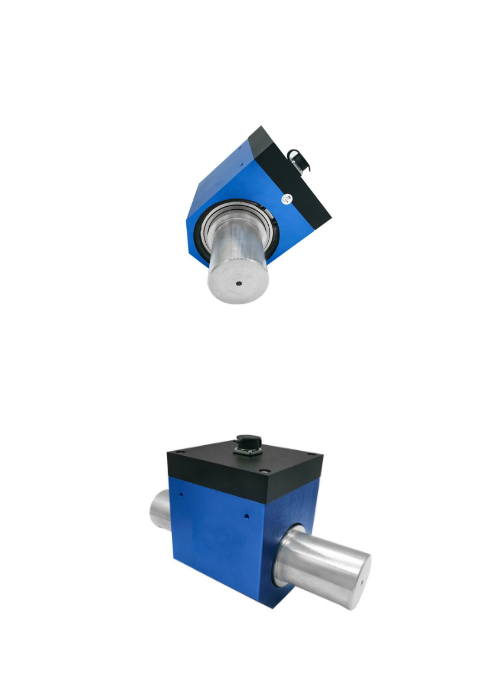
Characteristics of Shaft Torque Sensors
- Direct Measurement: Shaft torque sensors measure torque directly on the rotating shaft. This means they provide real-time data which is crucial for monitoring and controlling systems.
- High Accuracy: These sensors are known for their high precision, delivering reliable data for various applications.
- Wide Range: Shaft torque sensors can measure a wide range of torques. Making them versatile for different needs.
- Rugged and Durable: Designed to withstand the harsh conditions of a rotating shaft. These sensors are typically rugged and durable. Ensuring they deliver accurate results over time.
- Compact Size: Many shaft torque sensors are compact, which allows them to be installed in areas with limited space.
- Easy Integration: These sensors can often be easily integrated into existing systems, saving time and resources in setup.
Remember, these are general characteristics. Specific features can vary depending on the particular model or manufacturer.
At Sino-Inst, we offer a variety of shaft torque sensors, each with their own unique benefits, to ensure you get the perfect fit for your specific needs.
Featured Torque Sensors
Where are Shaft Torque Sensors Used? Real-World Applications
Automotive Industry:
Shaft torque sensors play an integral role in the automotive sector. They are extensively used to measure engine output, drivetrain performance, and for electric power steering systems. Accurate torque measurements can lead to improvements in the vehicle’s fuel efficiency and overall performance.
Manufacturing and Assembly Lines:
Shaft torque sensors are vital in automated assembly systems, including manufacturing of appliances, electronics, and automobiles. They ensure that screws, bolts, and other fasteners are tightened with the correct amount of torque, thereby maintaining the quality and integrity of the product.
Renewable Energy:
In wind turbines, shaft torque sensors measure the power output, helping in efficient power generation and early detection of system failures. This contributes to the reliability and longevity of these renewable energy systems.
Aerospace:
Shaft torque sensors are used in the testing and maintenance of aircraft engines and components. They provide valuable data to ensure the efficiency and safety of the aircraft.
Maritime Applications:
In the maritime industry, shaft torque sensors are used to monitor the performance of ship propellers, optimizing fuel consumption, and diagnosing potential issues.
These examples are based on general knowledge and industry practices. At Sino-Inst, we can offer tailored solutions and consultations to meet your specific needs.
Choosing the Perfect Shaft Torque Sensor: Key Factors to Consider
Absolutely, selecting the ideal shaft torque sensor involves many considerations to ensure it performs well in its intended application. Here are some of the key factors you should take into account:
- Measurement Range: The sensor should have the capacity to measure the maximum torque that will be applied to the shaft without going beyond its limit.
- Accuracy: Consider the sensor’s accuracy and resolution. You want a sensor that can measure torque with the degree of precision required for your specific application.
- Installation Requirements: Make sure the sensor can be installed onto your existing shaft without requiring significant modifications to your machinery.
- Environment: The sensor should be able to withstand the environmental conditions it will be exposed to, such as temperature, humidity, vibration, and dust.
- Output Signal: Depending on your system, you might need a sensor with a specific type of output signal (analog, digital, wireless, etc.).
- Size and Weight: The sensor’s size and weight might be a crucial factor, particularly in applications where space is limited or in dynamic applications where the sensor’s weight could influence the measurement.
- Cost: Last but not least, consider the cost of the sensor and whether it fits within your budget.
These considerations can guide you in selecting the right shaft torque sensor for your specific needs. Remember, the best sensor is not always the most expensive one, but the one that is most suited to your application and environment.
Maintaining Your Shaft Torque Sensor
Maintaining your shaft torque sensor is crucial to ensure its longevity and performance. Here are some essential tips to help you get the most out of your sensor:
By following these tips, you can maximize the lifespan and performance of your shaft torque sensor, ultimately saving time and resources in the long run.
FAQ
More Torque Measurement Solutions
Shaft torque sensors are remarkable devices that play a critical role in many industries. By understanding how they work and choosing the right one for your needs, you can greatly enhance the efficiency, safety, and reliability of your operations.
At Sino-Inst, we offer a range of high-quality, customizable shaft torque sensors. As experienced manufacturers and suppliers, we’re here to help you find the perfect solution to meet your needs. Contact us to learn more about how our products can enhance your operations.
Request a Quote
Wu Peng, born in 1980, is a highly respected and accomplished male engineer with extensive experience in the field of automation. With over 20 years of industry experience, Wu has made significant contributions to both academia and engineering projects.
Throughout his career, Wu Peng has participated in numerous national and international engineering projects. Some of his most notable projects include the development of an intelligent control system for oil refineries, the design of a cutting-edge distributed control system for petrochemical plants, and the optimization of control algorithms for natural gas pipelines.