Looking for a specific type or a custom continuous liquid level sensor? Sino-Inst offers High quality Liquid level sensors for continuous level measurement.
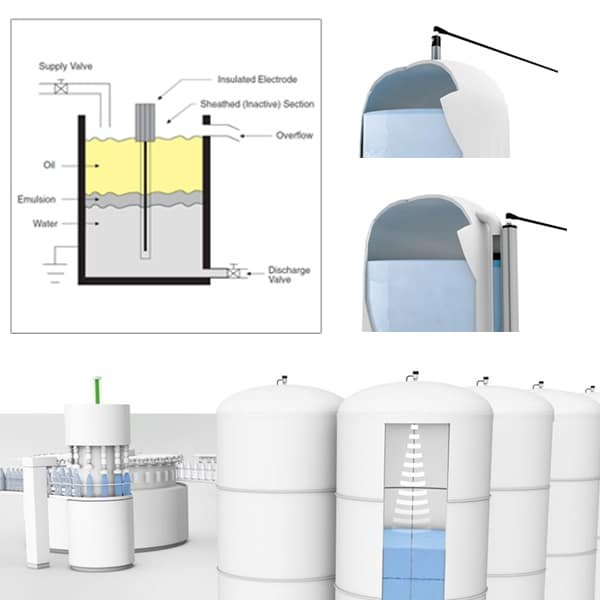
Level sensors are used in process control in many industries and they fall into two categories. Continuous level measurement sensors and Point level measurement sensors.
The point level measurement sensor is used to indicate a single discrete level, that is, to indicate a preset level. The function of this type of sensor is the upper limit alarm, which indicates the overfill condition, or the lower limit alarm condition.
Continuous level sensors are more complex, allowing level monitoring of the entire system. They measure the level of the liquid level in a range, not the level of a point. Continuous level sensors produce an analog output that is directly related to the liquid level in the container. To build a level measurement system, this output signal is transmitted to the process control loop and visual indicators.
Sino-Inst offers a variety of Level senors for Continuous level measurement. If you have any questions, please contact our sales engineers.
Featured Continuous Level Sensors
What is a Continuous Liquid Level Sensor?
Continuous level sensor definition
Continuous level sensors are transmitters that measure liquids within a specified range. Level sensors determine the exact amount of liquid that provides a continuous analog signal. The level signal can be displayed directly on site or integrated into a process control or management system. These products can be installed vertically and horizontally. They are ideal for monitoring liquids in confined or restricted areas.
Wikipedia: Level sensor
Difference between a point level sensor and a continuous level sensor?
Point level sensor
A sensor designed for point detection will detect liquid at a certain point in the tank or chamber. Generally, this applies to processes that require high-level or low-level management.
In most cases, they act as switches when the tank level rises or falls to a certain level. This could be an alarm or a bonding device. Essentially, the sensor detects when the liquid has reached the desired point, and it acts as a switch to activate the necessary response.
Continuous level sensor
The continuous level sensor is designed to detect the level through every point in the tank or chamber. This means that it provides feedback regardless of the level and the entire container range. This is great for processes where level is always important, and for applications that require increased accuracy.
Read more about: Ultrasonic Level Sensors for Liquids Applications
Extended Reading: How to Measure Volume of Liquid
Extended reading: How does a Radar Corrosive Liquid Chemical Level Sensor work?
Continuous level sensor 4-20 ma
Sino-Inst provides signal output for all continuous level sensors. Analog signal output, 4-20mA output, 0-5V, RS485, HART optional.
Advantages of current signal (4 ~ 20mA signal)
- The current signal is suitable for long-distance transmission. Because the current signal is not affected by the resistance of the wire. And the voltage signal will be divided when the wire itself has resistance, resulting in inaccurate measurement. Generally, the maximum transmission distance of 4 ~ 20mA is controlled within 100m, and it is recommended to use digital signals (485 communication)
- The current signal generally uses a two-wire system, and the voltage signal generally uses a three-wire system. In contrast, the two-wire system saves materials and reduces costs than the three-wire system.
- Compared with the on-site working conditions, the anti-interference ability of the current signal is stronger than the voltage signal. In the case of interference, it is recommended that the user select a 4 ~ 20mA signal.
- The current signal can appropriately exceed the range of the range and output inaccurate signals. For example, a pressure transmitter with a range of 1MPa and an output of 4-20mA can output 24mA when it exceeds the range. The voltage signal is slightly different depending on the power supply. For example, a pressure transmitter with a range of 1 MPa and an output of 0 to 10 V cannot output signals above 9 V when the power supply is 9 V.
- When the wire materials are not the same (such as copper, nickel), a magnetic field will generally be generated. And the voltage signal will have an error, and the current signal will not be required in the case of higher accuracy requirements.
Continuous Level Sensor can also be used with paperless recorder.
Measuring techniques for continuous level measurement
1. Ultrasonic Level Sensors
Ultrasonic Level Transmitters provide non-contact and maintenance-free level measurement, (Like the Radar ) for fluids, pastes, sludges and powdery to coarse bulk materials.
Ultrasonic level measurement, easy installation, wireless, portable and can be explosion-proof.Sonic is the sound we can hear. Ultrasonic is the sound above the human hearing range.
A human can hear maximum up to a frequency of 20 KHz. Ultrasonic frequencies are above 20 KHz. Ultrasonic waves are used to measure the level of liquids and solid objects in industries.
Ultrasonic level measurement is the contactless principle and most suitable for level measurements of hot, corrosive and boiling liquids.
The normal frequency range used for ultrasonic level measurements is within a range of 40-200 KHz.
Extended reading: Ultrasonic liquid level sensors
2. Hydrostatic (Pressure) Level Transmitters
Hydrostatic level transmitters, also called submersible level transmitter, or pressure level transmitters. For Hydrostatic level measurement, Continuous level measurement in liquid applications with pressure sensors. These transmitters help in determining fluid level of a container. By measuring the pressure of resting body of the fluid within it.
3. Continuous Level Radar Sensors
Radar level transmitter, also called Radar level gauge. Non-contact Continuous level measurement in liquids and solids with free space radar sensors.
Non-contacting radar, based on microwave technology, detects only surfaces that reflect energy. These transmitters work on the principle of radar by using radio wave emissions. Mounted at the top of a tank filled with a liquid.
The transmitter sends a radar signal into the liquid and receives a reflection of the signal. The transmitters then analyze the current fill level of the tank based on the time taken by the transmitted signal to return.
Extended reading: Radar Liquid Level Sensor|Corrosive, steam, volatile liquids
4. Guided Wave Radar Level Sensors
Guided Wave Radar (GWR) Level Transmitters, also called wave guided radar level transmitter. Using guided wave radar technology, GWR level transmittershave no moving parts. They can measure both level and the interface between two media.
Continuous level measurement in liquids and solids with guided wave radar sensors. These transmitters work by sending a microwave pulse through a sensor cable or rod. The signal hits the surface of the liquid, and travels back to the sensor, and then to the transmitter housing.
Based on the time taken by the signal to travel down the sensor and back up again. The electronics integrated in the transmitter housing determine the filling level.
Extended Reading: Silo/Bin material level measurement system
5. Capacitance level detectors
Capacitance level detectors, also known as Capacitance level transmitter. RF Capacitance Level Transmitter offers continuous and point level detection. In liquids and solids with capacitance probes.
These transmitters use liquid stored in a tank or container as a dielectric medium between two or more electrodes. The energy capacity of the capacitor circuit increases when there is more liquid, and decreases if there is less liquid. Measuring the variations in the capacitance value, capacitance level transmitters calculate level of the tank.
Read more about: Capacitive Level Measurement Principle.
6. Magnetostrictive level transmitter
Magnetostrictive level transmitter, in-tank liquid level transmitter, is a continuous magnetic level gauge. The magnetostrictive level sensor, measure the level of fluid in the vessel.
By detecting the level of the magnets contained within the float and then transmits the measurement back to the control system.
7. Magnetic Float level sensors
Magnetic Float level sensors are continuous level sensors featuring a magnetic float that rises and falls as liquid levels change.
The movement of the float creates a magnetic field that actuates a hermetically sealed reed switch located in the stem of the level sensor, triggering the switch to open or close.
Comparative analysis – 7 Tank Level Measurement Sensors
Applications
Continuous level sensors are versatile in monitoring liquid level needs. They can monitor water, diesel, lube oils and fuels, as well as various chemical and petrochemical liquids. And compatible with corrosive and non-corrosive substances.
Continuous level sensors are and used by industries including:
- Food and Beverage
- HVAC
- Medical
- Printing
- Off-Highway Vehicles
- Semiconductor
- Oil and Gas
- Agriculture
- Wastewater Treatment
- Concrete/Aggregate
- Plastic/Vinyl
- Marine
- Chemical
Extended reading: Sludge Blanket Level Detector Appliactions
How to select a continuous level sensor?
Selection of level measurement sensor.
Issues to consider before selecting a level measurement sensor include:
- Measure liquid or solid?
- What is the temperature and pressure range of the application environment?
- Need point level measurement or continuous measurement?
- What is the level measurement range required?
- Is the measured material conductive?
- Will the measured material cover or accumulate on the surface?
- Will there be turbulence, foam or steam on the liquid surface?
- Do you need contact or non-contact level measurement?
- What kind of output is required, analog, relay, digital display or other?
Extended Reading: Laser level transmitter working principle
Frequently
Asked
Questions
Technical Support
Sino-Inst offers over 40 Continuous Level Measurement Sensors. About 50% of these are liquid level meters, 40% is the tank level sensor.
A wide variety of Continuous Level Measurement Sensors options are available to you, such as free samples, paid samples.
Sino-Inst is a globally recognized supplier and manufacturer of Continuous Level Measurement Sensors instrumentation, located in China.
Request a Quote
Wu Peng, born in 1980, is a highly respected and accomplished male engineer with extensive experience in the field of automation. With over 20 years of industry experience, Wu has made significant contributions to both academia and engineering projects.
Throughout his career, Wu Peng has participated in numerous national and international engineering projects. Some of his most notable projects include the development of an intelligent control system for oil refineries, the design of a cutting-edge distributed control system for petrochemical plants, and the optimization of control algorithms for natural gas pipelines.