High Accuracy Pressure Transducers are also called high precision pressure transducers or high accuracy pressure sensors. Sino-Inst manufactures various types of High Accuracy Pressure Transducers.
From the perspective of accuracy, the accuracy of conventional pressure transmitters is 0.5%. Therefore, pressure transmitters can be divided into high-precision pressure transmitters (0.1% or 0.2% or 0.075%) and general pressure transmitters ( 0.5%).
High Accuracy Pressure Transducers support mV/V, V, mA and digital outputs. Ideal for applications requiring very high precision measurements such as oil, gas and geothermal energy exploration.
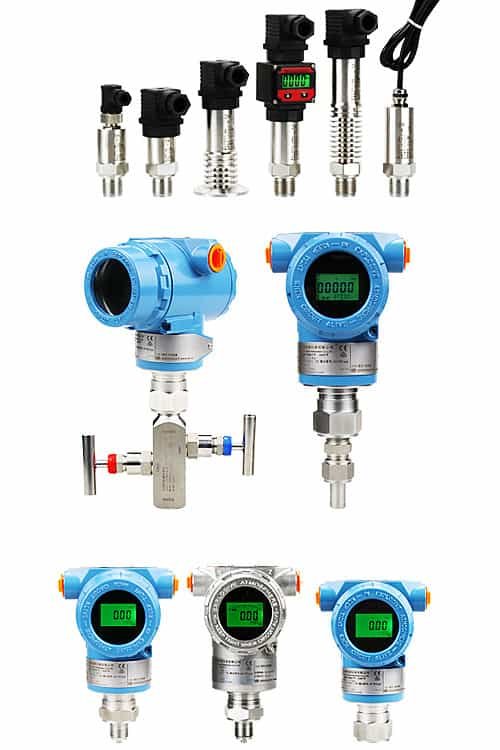
Featured High Accuracy Pressure Transducers for Sale
When ordering a pressure transmitter, you can often be asked what accuracy pressure transmitter you need. Then our sales engineer will tell you that we have 0.5% accuracy and 0.1% accuracy. Even higher precision ones can be customized.
Also, different accuracy may affect the price of the pressure transmitter. So what is the accuracy of the pressure transmitter? Do we need to blindly pursue higher-precision pressure transmitters?
Extended Reading: 4-20ma pressure transducer wiring diagram
What is the accuracy of a pressure transmitter?
The accuracy of the pressure transmitter is the same as that of all measurement and display instruments, and it is an indicator of the reliability of the measured value of the instrument.
The instrument has a maximum allowable error (deviation), and the probability of more than 98% of the results obtained from N times of measurements on the same measured value does not exceed this range.
Maximum allowable error / measuring range * % = meter accuracy
For a pressure transmitter with an accuracy of class 0.1,
Output allowable error = output range * instrument accuracy% = 16 * 0.001 = 0.016 (mA)
That is, the maximum possible error when this meter is measured is plus or minus 0.065mA.
Extended reading: Pressure Sensor Applications-Featured Industry Applications
Usually, when considering the overall accuracy of the pressure transmitter, the factors that affect the accuracy of the pressure transmitter generally need to be considered.
According to the experience of Sino-Inst, we believe that everyone should choose the tolerance of the pressure transmitter according to the requirements of the industrial process. Instead of selecting according to the pressure transmitter indicators installed in the field.
Extended reading: Water Pressure Sensors for Measurement of Water Pressure
Factors affecting the overall accuracy of pressure transmitters
Read more about: What Are 0-10V Pressure Transducers?
pressure transducer 4-20mA
Many friends have some misunderstandings about this issue, and feel that 4-20mAdc is more troublesome to calculate. So why use 4-20mAdc?
The field two-wire pressure transmitter needs power supply. First, it is necessary to ensure that there is still a certain current in the case of zero position. Then in the design, we found that the minimum starting current of the transmitter is 3.5mA, which means that the transmitter can still work under 3.5mA.
Then if it is 0mA, then there is no power supply and it cannot work.
So use 4mA as the zero position, if it starts at 0mA, the meter will not work. If there is a disconnection in the field, there is no way to tell if it is a problem with the meter or the power supply. Therefore, the international general standard starts from 4mA.
The second question, why is it 20mA? Why not 30mA? Why not 100mA?
It stands to reason that the bigger the better, the higher the resolution, but it is not.
Through the observation of the gas explosion point, it is found that the spark generated when the 20mA is switched on and off will not cause the gas explosion. 20mA is a critical value, so ≤20mA is safe. If >20mA, there will be an explosion problem, so 4-20mA is a better value.
Then there are also some occasions where 0-10mA is used, which is generally not used in the process industry. It may be used in the discrete industry. There are also some occasions where 0.5v-4.5v or 0-5v are used in the discrete industry. Then for the process industry, it is mainly 4-20mA.
Sino-Inst is a pressure transmitter manufacturer, the main products include intelligent pressure transmitter, digital pressure transmitter, high temperature pressure transmitter, sanitary pressure transmitter, compact pressure transmitter, liquid level pressure transmitter transmitter, differential pressure transmitter, etc., the product series is complete, high precision, welcome to inquire!
Extended Reading: Smart pressure transmitter
Frequently
Asked
Questions
More Pressure Measurement Solutions
Sino-Inst is Manufacturer of high accuracy pressure transducers. We supply more than 50 kinds of high accuracy pressure transducers. Including diffused silicon, single crystal silicon, capacitive and other types of pressure transmitters.
High accuracy pressure transducers are used in automatic process control pressure measurement of liquid metallurgy, machinery, petroleum, electric power, chemical industry, compressor, light industry, textile, steam, sewage treatment equipment, heat transfer oil, etc.
It has good water resistance, small size, high cost performance and easy installation. The shell is made of stainless steel, which has good sealing, vibration resistance, stable and reliable performance.
Sino-Inst’s High accuracy pressure transducers, made in China, Having good Quality, With better price. Our pressure measurement instruments are widely used in China, India, Pakistan, the US, and other countries.
The entire team at Sino-Inst’s has received excellent training, so we can ensure that every client’s needs are met. For assistance with your product requirements, whether it’s a High accuracy pressure transducer, level sensor, or other device, give us a call.
Request a Quote
Wu Peng, born in 1980, is a highly respected and accomplished male engineer with extensive experience in the field of automation. With over 20 years of industry experience, Wu has made significant contributions to both academia and engineering projects.
Throughout his career, Wu Peng has participated in numerous national and international engineering projects. Some of his most notable projects include the development of an intelligent control system for oil refineries, the design of a cutting-edge distributed control system for petrochemical plants, and the optimization of control algorithms for natural gas pipelines.