Explosion proof ultrasonic level sensor is a non-contact, easy to install and maintain liquid level measurement instrument.
It is used to measure flammable and explosive liquids such as diesel oil and crude oil. Or used to measure the height of liquids in explosion-proof environments. It is widely used in explosion-proof environments such as oil exploration, oil refining, chemical industry, and medicine.
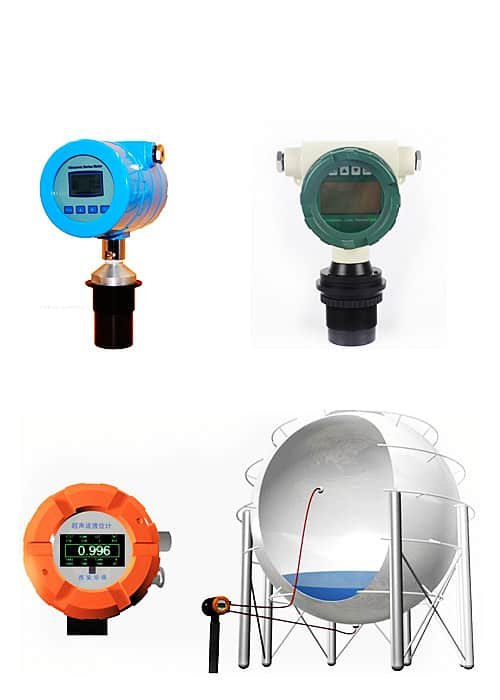
Featured Explosion Proof Ultrasonic Level Sensors
Intrinsically Safe/Explosion Proof
It is often necessary to use explosion-proof instruments in industrial sites. The general industrial explosion-proof instruments are mainly explosion-proof and intrinsically safe. So, how to understand the difference between them?
Read more about: What Is the Difference Between Class 1 Div 1 and Class 1 Div 2 ?
Two-wire Explosion Proof Ultrasonic Level Sensor
- Measurement range: 5m, 10m, 15m, 25m (selected according to the actual measurement range)
- Blind area: 0.25m~0.8m
- Ranging accuracy: 0.25% to 0.5% (standard conditions)
- Ranging resolution: 1mm
- Pressure: Below 4 atmospheres
- Instrument display: Built-in LCD to display liquid level or space distance
- Analog output: 4~20mA
- Digital output: none
- Power supply voltage: DC24V/1W, built-in lightning protection device
- Ambient temperature: -20℃~+60℃ High temperature needs to be customized (customizable temperature resistance 90℃)
- Protection class: IP65 or IP68
Extended reading: Case Study: Automatic Sludge Blanket Level Detector
Four-wire Explosion Proof Ultrasonic Level Sensor
- Measurement range: 5m, 10m, 15m, 25m (selected according to the actual measurement range)
- Blind area: 0.25m~0.8m
- Ranging accuracy: 0.25% to 0.5% (standard conditions)
- Ranging resolution: 1mm
- Pressure: Below 4 atmospheres
- Instrument display: Built-in LCD to display liquid level or space distance
- Analog output: 4~20mA
- Digital output: RS485, Modbus protocol or custom protocol
- Relay output: two independent outputs
- Power supply voltage: DC24V/AC220V, built-in lightning protection device
- Ambient temperature: -20℃~+60℃ High temperature needs to be customized (customizable temperature resistance 90℃)
- Protection class: IP65 or IP68
More about Factors To Consider When Choosing Explosion Proof Ultrasonic Level Sensors.
External Explosion Proof Ultrasonic Level Sensor
- Range specifications optional: 3m, 5m, 10m, 20m, 30m
- Display resolution: 1mm
- Short time repeatability: 1mm
- Measurement error: ±1‰FS (too thick tank wall, unstable pressure and temperature may affect the accuracy)
- Migration amount: ±10 m
- Current output: 4~20mA, maximum load 750Ω
- Communication: RS-485, infrared interface
- The ambient temperature of the liquid level gauge host: -30℃~+70℃
- Ultrasonic probe using ambient temperature: -50℃~+100℃, (wide temperature probe can be provided according to customer needs)
- Operating environment humidity: 15%~100%RH
- Explosion-proof mark: Ex d IIC T6 Gb
- Shell protection: IP67
- Liquid level display: 6-digit OLED display (unit: m)
- Blind zone: There is a measurement blind zone in the ultrasonic level gauge
Extended reading: Non contact level measurement
Ultrasonic Level Sensor Working Principle
The working principle of the ultrasonic liquid level sensor is:
Ultrasonic transducer (probe) emits high-frequency pulse sound waves, and the surface of the measured level (material) is reflected back. The reflected echo is received by the transducer and converted into an electrical signal. The propagation time of the sound wave is proportional to the distance from the sound wave to the surface of the object.
The relationship between the sound wave transmission distance S and the sound speed C and the sound transmission time T can be expressed by the formula: S=C×T/2.
The probe part emits ultrasonic waves, which are then reflected by the liquid surface. The probe part is received again. The distance from the probe to the liquid (object) surface is proportional to the elapsed time of the ultrasonic wave:
hb = CT2
Distance [m] = time × speed of sound/2 [m]
The temperature compensation formula of sound velocity:
Ambient sound velocity = 331.5 + 0.6 × temperature
Extended reading: Amazing Solutions for Continuous Liquid Level Measurement
Ultrasonic Level Sensor for Tanks
Ultrasonic fuel tank level sensor, also called non-contact fuel meter. Ultrasonic level sensor measure continuous liquid level, fluid level, or oil level.
Ultrasonic level sensors measure the distance between the transducer and the surface. Using the time required for an ultrasound pulse to travel from a transducer to the fluid surface and back (TOF). These sensors use frequencies in the tens of kilohertz range; transit times are ~6 ms/m. The speed of sound (340 m/s in air at 15 degrees C, 1115 fps at 60 degrees F) depends on the mixture of gases in the headspace and their temperature.
More about Ultrasonic level measurement
Ultrasonic sensors work without the need to touch the medium being measured. Ultrasonic sensors are ideal for difficult or corrosive liquids such as acids, wastewater, and others. Ultrasonic level sensors are also ideal for continuous level measurement. While float switches and other sensors are adept at measuring when liquid levels are above or below a certain point. The nature of ultrasonic level measurement is such that levels can be sensed and displayed in real-time.
Read more about: Top 5 Ultrasonic Level Sensor Applications
Features of Ultrasonic Tank Level Sensor:
- Non-contact – nothing touches the liquid
- Easy to install at the top of the tank into standard fittings
- Use indoors or outside, in metal or plastic tanks
- Connects to other industrial equipment
- Measures a wide variety of liquids and liquid environments
- Accessories to display, alarm, and control liquid levels
- Wireless option sends tank levels to a LAN or the cloud
- MRO & OEM tank setup duplication without re-calibration
Read more about: Ultrasonic Tank Level Sensor-External Mounted
Frequently
Asked
Questions
More Explosion Proof Transmitters
Related Blogs
Sino-Ins offers 20 Explosion Proof Ultrasonic Level Sensors products.
About 13% of these are ultrasonic level transducers, 4% are ultrasonic level indicators.
A wide variety of Explosion Proof Ultrasonic Level Sensor options is available to you, such as free samples, paid samples.
Sino-Inst is an Explosion Proof Ultrasonic Level Sensor supplier, located in China.
Explosion Proof Ultrasonic Level Sensor products are most popular in North America, Mid East, and Eastern Europe.
The United States, and India, which export 99%, 1%, and 1% of ultrasonic level transmitters respectively.
You can ensure product safety by selecting from a certified supplier, with ISO9001, ISO14001 certification.
Request a Quote
Wu Peng, born in 1980, is a highly respected and accomplished male engineer with extensive experience in the field of automation. With over 20 years of industry experience, Wu has made significant contributions to both academia and engineering projects.
Throughout his career, Wu Peng has participated in numerous national and international engineering projects. Some of his most notable projects include the development of an intelligent control system for oil refineries, the design of a cutting-edge distributed control system for petrochemical plants, and the optimization of control algorithms for natural gas pipelines.