Fluid level measurement is a crucial, yet often overlooked, process spanning various industries, from manufacturing to oil and gas. Methods for measuring fluid levels have come a long way, evolving from basic sight glass to advanced techniques like ultrasonic or radar measurement. Each method has its merits, and the choice often hinges on the specific scenario. Join us as we delve into these fascinating techniques, their advantages and shortcomings, in our comprehensive guide to fluid level measurement.
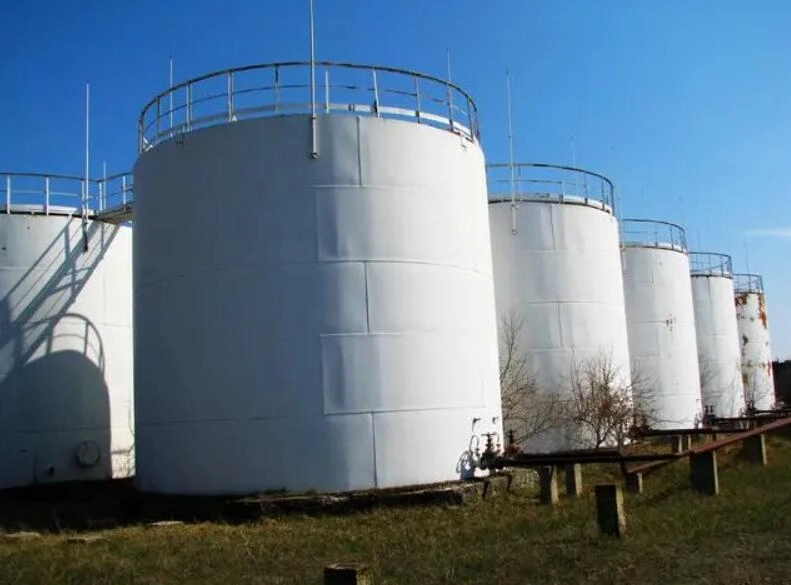
The Basics of Fluid Level Measurement
Let’s take a step back and delve into what fluid level measurement truly entails. The fluid can be anything – water in a reservoir, oil in a barrel, or a beverage in a production line. And the ‘tool’ we’re referring to? That’s the method of measurement.
Selecting the right method isn’t a random choice but requires careful consideration of both the fluid (target medium) and the container (vessel). Why? Because different fluids and containers can impact the measurement’s accuracy. Think about it this way – measuring the level of water in a glass is a much simpler task than assessing oil quantity in a massive industrial tank. The right method ensures the measurements are not only accurate but precise.
Now, let’s briefly introduce the main methods used for this purpose. There are six principal techniques, each boasting its unique strengths and limitations:
- Continuous Float Level Transmitters: Utilizes a float that moves with the fluid level, providing continuous measurement.
- Differential Pressure Transmitters: Measures the pressure difference at two points in the fluid, correlating it with the fluid level.
- Load Cells: Uses force measurement to deduce the fluid level.
- Radar Level Transmitters: Leverages radio wave technology to determine the fluid’s distance from the sensor, thus the fluid level.
- Radio Frequency (RF) Capacitive Level Transmitters: Employs the change in capacitance caused by the change in fluid level to provide measurement.
- Ultrasonic Level Transmitter: Sends ultrasonic pulses towards the fluid surface and calculates the fluid level based on the time it takes for the pulses to return.
With the basics covered, let’s delve deeper into these methods, their applications, and how to decide which one is the ‘perfect tool’ for your ‘task’. Stay tuned!
Traditional Methods of Fluid Level Measurement
Before we journey into the modern age of fluid level measurement, it’s worth taking a moment to appreciate the tried-and-true traditional methods that have served various industries for decades. Two of the most common methods include sight glass and hydrostatic pressure measurements.
Sight Glass Measurement
The sight glass method is a simple yet effective method for fluid level measurement. Picture a transparent tube attached to a tank, with the fluid level in the tube reflecting the fluid level in the tank. By observing the fluid in the sight glass, operators can visually estimate the fluid level in the tank.
The pros of this method are its simplicity and directness. There’s no need for complex calculations or advanced technology, making it both reliable and cost-effective. It’s especially useful for tanks containing multiple liquids of different densities, as the distinct separation layers can be easily seen.
However, the sight glass method also has its cons. Its simplicity can be a limitation in situations where precise measurement is necessary. Furthermore, it can be challenging to use in high-pressure tanks or with opaque or highly viscous fluids. Also, the physical wear and tear on the sight glass can lead to reading inaccuracies over time.
Hydrostatic Pressure Measurement
Hydrostatic pressure measurement operates on the principle that the pressure at any point in a fluid is directly proportional to its height. Thus, by measuring the pressure at the bottom of a tank, we can calculate the fluid’s height.
One of the key advantages of this method is its versatility. It can measure fluid levels in both open and closed tanks and handle various fluid types, from water to oil. Additionally, it offers consistent readings and can handle extreme temperatures and pressures.
Nevertheless, the hydrostatic method is not without its drawbacks. Changes in the fluid density can affect the accuracy of readings. Moreover, it requires regular maintenance and calibration to ensure accurate measurements, especially when dealing with corrosive or high-temperature fluids.
These traditional methods have laid a strong foundation for fluid level measurement. However, as with any technology, advancements were inevitable and necessary. Next, we’ll look at more sophisticated methods that leverage technological progress to improve accuracy and versatility in fluid level measurement. Stay with us!
Advanced Techniques in Fluid Level Measurement
Technological advancements have gifted the world of fluid level measurement with high-precision tools like ultrasonic sensors, radar measurement devices, and capacitive level transmitters. These tools elevate our ability to track fluid levels accurately and efficiently. Let’s learn more about them.
Ultrasonic Level Measurement
Ultrasonic level measurement capitalizes on sound wave technology. An ultrasonic sensor, located at the top of a tank, sends sound waves downward. When these waves hit the fluid surface, they bounce back to the sensor. The sensor then calculates the time taken for this round trip, which directly relates to the fluid level.
Pros: Ultrasonic sensors are non-contact devices, making them perfect for hazardous or corrosive fluids. These sensors are highly accurate and work well under various environmental conditions.
Cons: However, factors like a foamy fluid surface, intense turbulence, or heavy vapors can hamper the accuracy of ultrasonic measurements. Also, ultrasonic sensors are generally more expensive than traditional measurement methods.
Radar Level Measurement
Radar level measurement also uses the principle of echo, but instead of sound waves, it employs radio waves. These waves are released by a radar sensor, bounce off the fluid surface, and return to the sensor. The duration of this round trip helps calculate the fluid level.
Pros: Radar sensors are extremely accurate and can operate under a wide range of temperatures and pressures. They offer non-contact measurement, which is advantageous when dealing with dangerous or corrosive fluids.
Cons: While highly reliable, radar sensors are complex and more costly to install and maintain. They may also encounter difficulties in tanks with heavy internal structures due to signal interference.
Capacitive Level Measurement
Capacitive level measurement works by detecting changes in an electric field. A probe inserted into a tank forms one plate of a capacitor, with the tank wall (or a reference probe) serving as the other plate. As the fluid level changes, the dielectric constant changes, leading to a change in capacitance which can be measured and related to the fluid level.
Pros: Capacitive level transmitters are versatile, able to measure the levels of a wide range of fluids, including those that are corrosive, viscous, or have a low dielectric constant. They also function well in high-pressure or high-temperature environments.
Cons: However, they can be influenced by buildup on the probe or changes in the fluid’s dielectric constant. They also require regular calibration for maintaining their accuracy.
With these advanced techniques at our disposal, the landscape of fluid level measurement has broadened, offering more precision and flexibility than ever before. However, choosing the right method always depends on your specific requirements. In the following section, we’ll help guide you in making this choice. Stay tuned!
Choosing the Right Method for Fluid Level Measurement
In the world of fluid level measurement, some factors will influence the selection.
Type of Fluid: Different fluids have different properties that can affect the measurement accuracy. For instance, ultrasonic sensors may not be the best choice for highly viscous or foamy fluids due to signal dispersion. For such fluids, capacitive level transmitters might offer more reliable results.
Size of the Container: The size and shape of the container can also influence the choice of measurement method. For example, sight glass measurement might be perfect for small tanks, while radar or ultrasonic measurements could be better suited for large industrial tanks.
Environmental Conditions: The measurement method must also take into account environmental conditions. If the tank is in a high-temperature or high-pressure environment, robust methods like hydrostatic pressure or capacitive level measurement would be advantageous.
Industry Requirements: Lastly, industry-specific needs play a role. For instance, in the food and beverage industry, non-contact methods are often preferred to prevent contamination. While in the oil and gas industry, methods capable of withstanding corrosive materials are necessary.
More Level Measurement Solutions
Grain Bin Level Indicators: The Missing Piece in Your Grain Storage Solution
Radar Antenna Types for Radar Level Meters: How to Choose?
Radar Liquid Level Sensors
Top Powder Level Sensors-How to Choose
Ultrasonic Tank Level Sensors for Tank Level Monitoring
Ultrasonic Level Sensors for Liquids: The Key to Precise & Efficient Measurements
In conclusion, there’s no one-size-fits-all solution in fluid level measurement. It’s a careful selection process that requires a deep understanding of the application, environment, and industry needs. By considering these factors and weighing the pros and cons of each method, you can make an informed decision that ensures accurate, reliable, and efficient fluid level measurement.
The world of fluid level measurement is both vast and varied. From traditional methods like sight glass and hydrostatic pressure to modern techniques employing ultrasonic, radar, and capacitive technologies, the tools at our disposal are as diverse as they are dynamic.
With Sino-Inst by your side, you get more than just a product – you get a commitment to quality, a dedication to precision, and most importantly, a partner who understands and respects the importance of your work.
Ready to take the next step in your fluid level measurement journey? Get in touch with us today. Let’s explore the possibilities together and unlock the full potential of fluid level measurement for your operations.
Contact Sino-Inst: Your trusted partner in fluid level measurement.
Request a Quote
Wu Peng, born in 1980, is a highly respected and accomplished male engineer with extensive experience in the field of automation. With over 20 years of industry experience, Wu has made significant contributions to both academia and engineering projects.
Throughout his career, Wu Peng has participated in numerous national and international engineering projects. Some of his most notable projects include the development of an intelligent control system for oil refineries, the design of a cutting-edge distributed control system for petrochemical plants, and the optimization of control algorithms for natural gas pipelines.