Ultrasonic level sensors for liquids have revolutionized the way we measure and manage fluid levels in various industries. By leveraging advanced technology, these sensors offer unparalleled accuracy and efficiency in liquid level measurement. In this article, we’ll delve into the principles, benefits, and applications of ultrasonic level sensors, explore some best practices for their use, and provide practical examples and data to illustrate their effectiveness.
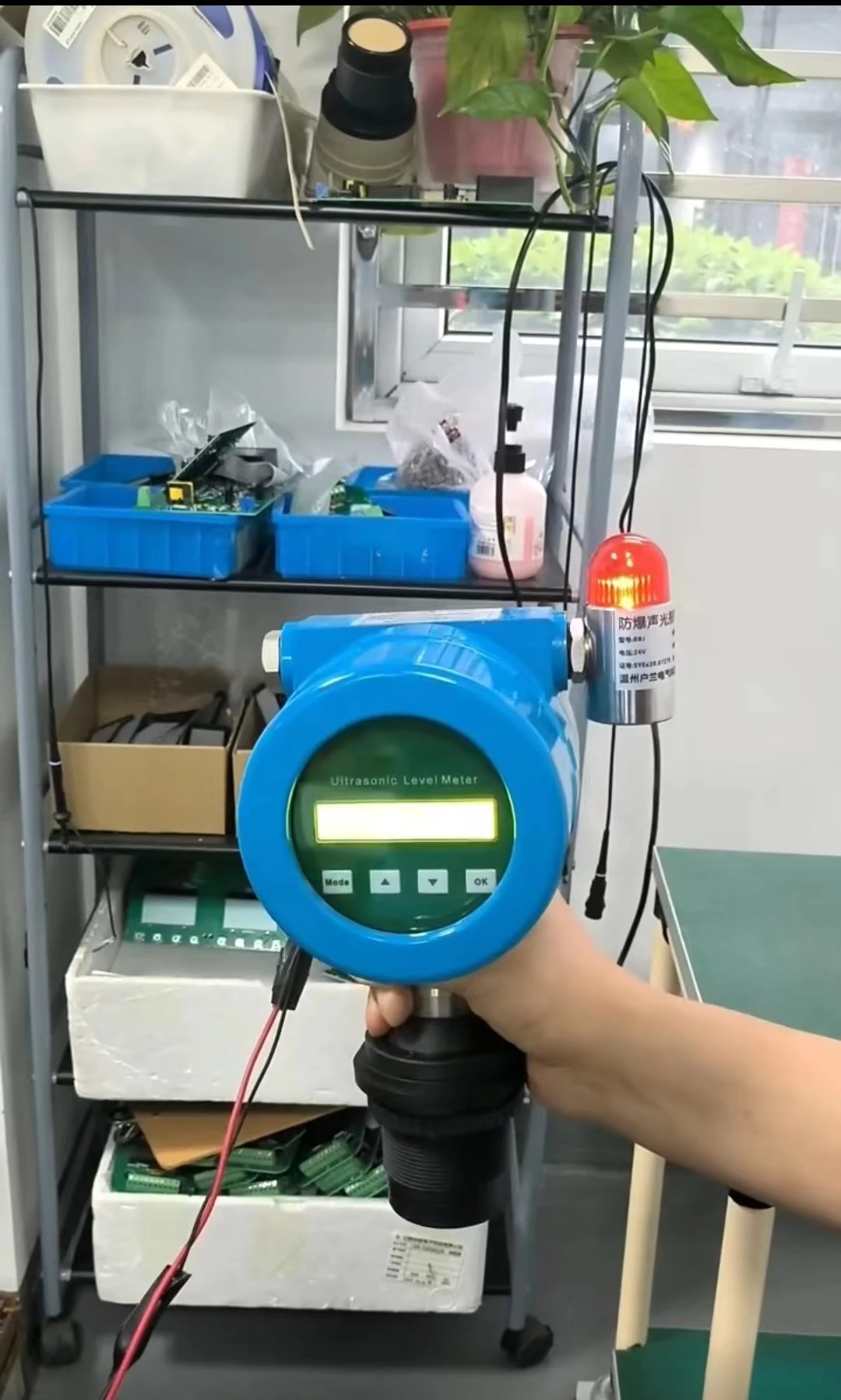
Learn more about other level measurement technologies in our comprehensive guide.
What Are Ultrasonic Level Sensors for Liquids?
This technology provides continuous level measurement, making it ideal for monitoring liquid levels in tanks, reservoirs, and other containers.
Ultrasonic sensors are known for their reliability, accuracy, and ease of installation, making them a popular choice for various industries.
How Do Ultrasonic Level Sensors Work?
The principle behind ultrasonic level sensors is the time-of-flight method.
The sensor emits an ultrasonic pulse, which travels through the air and reflects off the liquid surface. The sensor then receives the reflected echo and calculates the time taken for the pulse to travel to and from the surface.
By knowing the speed of sound in the air and the time taken for the pulse to return, the sensor can accurately determine the distance to the liquid surface and thus calculate the liquid level.
The relationship between the sound wave transmission distance S and the sound speed C and the sound transmission time T can be expressed by the formula: S=C×T/2.
Advantages of Ultrasonic Level Sensors
- Non-contact measurement: Since ultrasonic sensors do not need to come into direct contact with the liquid, they are less susceptible to wear and tear, reducing maintenance requirements.
- High accuracy: Ultrasonic level sensors offer excellent accuracy, typically within ±0.25% of the measured range. This level of precision makes them suitable for applications where precise measurements are crucial.
- Versatile applications: These sensors can be used for various liquids, including corrosive or viscous fluids, and are suitable for a wide range of industries, such as water treatment, oil and gas, food and beverage, and pharmaceuticals.
- Easy installation: Ultrasonic sensors are relatively easy to install, as they can be mounted on the top or side of a container without the need for extensive modifications.
- Cost-effective: Compared to other liquid level measurement technologies, ultrasonic level sensors offer an affordable solution that delivers reliable results.
Discover more applications and industries that benefit from ultrasonic level sensors.
Ultrasonic Level Sensors for Liquids Applications
Below, we provide a more in-depth look at specific applications of ultrasonic level sensors for liquids, including real-life measurement data where possible.
Wastewater Treatment Plant
In a wastewater treatment plant, ultrasonic level sensors are installed to monitor the water level in primary and secondary clarifiers. These sensors help maintain optimal operation by ensuring that the water levels remain within the desired range. For example, an ultrasonic level sensor with a measurement range of 0 to 10 meters can accurately monitor water levels with a resolution of 1 mm, allowing operators to make precise adjustments to the water inflow and outflow rates.
Diesel Storage Tank
In facilities that store and handle diesel fuel, it is crucial to monitor the liquid level in storage tanks to maintain accurate inventory management and prevent environmental hazards. Explosion-proof ultrasonic level meters are specifically designed to operate in potentially hazardous wherek the envi of igniting flammable vapors.
An explosion-proof ultrasonic level meter with a measurement range of 0 to 20 meters can be installed on a diesel storage tank with a capacity of 75,000 liters. The sensor provides continuous level readings, allowing operators to manage risk fuel inventory effectively and reduce the overfilling or spills.
Our customers have even configured our volumetric recorders for ultrasonic level meters. It can effectively monitor the tank volume.
FAQ
Tips for Choosing the Right Ultrasonic Level Sensor
To select the most suitable ultrasonic level sensor for your application, consider the following factors:
- Measurement range: Determine the required measurement range based on the size of your container or tank and the desired level of accuracy.
- Material compatibility: Ensure the sensor materials are compatible with the liquid being measured, particularly if it is corrosive or abrasive.
- Installation requirements: Consider the available mounting options, such as top or side mounting, and any space constraints in your application.
- Environmental conditions: Evaluate the operating temperature, humidity, and potential presence of dust, dirt, or other contaminants that may impact sensor performance.
- Output options: Choose an ultrasonic level sensor with the appropriate output options, such as 4-20 mA, RS-485, or HART, based on your system’s requirements.
Ultrasonic level sensors for liquids offer a reliable and accurate solution for monitoring and managing fluid levels in various industries. By understanding the technology, benefits, and applications of these sensors, you can make informed decisions to optimize your liquid measurement processes.
At Sino-Inst, we are experienced manufacturers and suppliers of ultrasonic level sensors and other measurement instruments. We offer customizable solutions to meet your specific application needs. If you’re looking for a reliable partner to support your liquid level measurement requirements, look no further.
Contact us today to discuss your ultrasonic level sensor needs and discover how our expertise can benefit your business.
Request a Quote
Wu Peng, born in 1980, is a highly respected and accomplished male engineer with extensive experience in the field of automation. With over 20 years of industry experience, Wu has made significant contributions to both academia and engineering projects.
Throughout his career, Wu Peng has participated in numerous national and international engineering projects. Some of his most notable projects include the development of an intelligent control system for oil refineries, the design of a cutting-edge distributed control system for petrochemical plants, and the optimization of control algorithms for natural gas pipelines.