Float Switch for Water Tank is a switch that can adjust the liquid level status of water tanks, buckets, pools and other fields. It can also be used to control and protect the motor of submersible pumps. The float level switch has the advantages of automatic adjustment, easy installation, reliable quality, stable operation, non-toxic and pollution-free, and affordable price. Therefore, it is widely used in homes, factories, mines and other places.
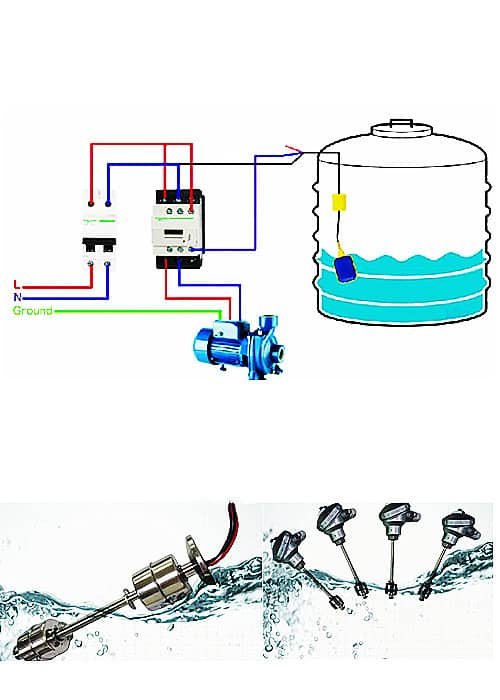
What Is a Float Switch?
Level switches can be electronic or mechanical. But it serves only one purpose – to alert you if it detects the presence of a product. so that you can act on this alert. A float switch is the switch that does this while floating on water or other liquid in the tank.
The float level switch is operated by magnetic force, without mechanical connection parts, and the operation is simple and reliable. When the float switch is measured medium floating float. The float drives the main body to move. At the same time the magnet on the other end of the float will control the magnet on the switch action lever.
Besides Float Switch, Submersible Level Transducer is also the First Choice for water level measurement and control.
How Does a Float Switch Work?
Use the magnetic float of the float level switch to rise or fall with the liquid level. Activate the reed switch chip at the set position in the sensor detection tube. Sends a contact open (close) switching signal.
One or more reed switches are installed in a closed non-magnetically conductive tube. This tube is then passed through one or more hollow float balls with a ring magnet inside. The rise or fall of the liquid will drive the float to move up and down together. Thereby, the reed switch in the non-magnetically conductive tube can be pulled in or disconnected. to output a switch signal
The Advantages of a Float Switch
Technical advantages of float level switch: The float switch does not contain bellows, springs, seals and other components that cause failures. Instead, a straight float is used to drive the internal magnet of the switch, and the simple lever of the float switch makes the switch act instantly. The float cantilever angle limit design prevents the float from being vertical.
The float level switch is a simple structure, easy to use, safe and reliable level controller. It is faster than the general mechanical switch and has a long working life. Compared with electronic switches, it has the characteristics of strong resistance to load shock, and one product can realize multi-point control. It has been widely used in shipbuilding, papermaking, printing, generator equipment, petrochemical industry, food industry, water treatment, electrician, dye industry, hydraulic machinery and so on.
The float switch is a liquid level control device with simple structure, convenient use, safety and reliability. It has smaller volume, faster speed and longer service life than general mechanical switches. Compared with electronic switches, it has the characteristics of strong resistance to load shock.
Extended reading: Water Tank Level Controller
Types of Float Switches
Choosing the Right Float Switch for Water Tank
Choose a float level switch that suits you. It can save costs and ensure a long service life.
- Applicable media: clean water, sewage, oil and acid-base liquids below medium concentration. Choose plastic or stainless steel material respectively.
- Material. There are two kinds of stainless steel (maximum specification 304) and plastic PVC. According to the different materials, the temperature and pH are also different. It needs to be selected according to the actual environment.
- Working principle (the most important point). It is to use micro switch (plastic material) or mercury switch (stainless steel material) as contact parts. When the cable float rises at a certain angle with the weight as the origin, it usually moves slightly The rising angle of the switch is 28°±2°, and the rising angle of the mercury switch is 10°±2°. The switch will have ON or OFF signal output, which acts as an alarm.
- Operating temperature: The temperature resistance of conventional plastic cable liquid level switches is within 80 degrees. Stainless steel can be selected from 80 degrees and 120 degrees (depending on the selected wire).
- Connection method: direct wire or add flange and junction box.
- Outlet material. Generally, the plastic cable float switch is equipped with a low-temperature cable as standard. For stainless steel, you can choose a low-temperature sheathed cable or a high-temperature silicone cable. Special requirements can be customized.
- Voltage and current. The withstand voltage is 220V (it must be overloaded by an AC contactor). The rated current is 8A, and the rated heating current is 10A. Please pay attention to the voltage and current not exceeding. Otherwise, the switch will burn out.
- Outlet length. The length of the line is proportional to the depth of the liquid level you need to detect. For example, if it is necessary to detect three meters, the switch outlet should be at least four meters above. The lead length is generally: 3m\ 4m\ 5m, etc. If longer, it can be customized.
Extended Reading: 3 inch (3″) Water Flow Meter
Which Level Control Switch Is Better for the Sewage Pool?
Which level switch is better for the sewage pool?
To answer this question, you must first consider the environment. Consider whether it is domestic sewage or industrial sewage. Industrial sewage generally contains heavy metals and the like. General customers will require non-contact measurement. If there are not many impurities in domestic sewage, the input type can be used. If there are too many impurities, it is better to use non-contact type.
Sewage treatment should also have a recycling process. For example, some organic water collection in tanks. Generally, it is sufficient to use the input type. Next, pay attention to the following points:
- There are many impurities, non-contact;
- Strong corrosiveness, non-contact;
- Environmental pressure input type of foam ozone tank;
Extended reading: GWR Corrosive Liquid Chemical Level Sensor
Related Blogs
Sino-Inst offers over 10 Float Switches for Water Tanks.
About 50% of these are liquid level meters, 40% is the tank level sensor.
A wide variety of level meters options are available to you, such as free samples, paid samples.
Sino-Inst is a globally recognized supplier and manufacturer of level measurement instrumentation, located in China.
Request a Quote
Wu Peng, born in 1980, is a highly respected and accomplished male engineer with extensive experience in the field of automation. With over 20 years of industry experience, Wu has made significant contributions to both academia and engineering projects.
Throughout his career, Wu Peng has participated in numerous national and international engineering projects. Some of his most notable projects include the development of an intelligent control system for oil refineries, the design of a cutting-edge distributed control system for petrochemical plants, and the optimization of control algorithms for natural gas pipelines.