What is a Thermal Mass Flow Meter ?
The thermal mass flow meter is also called Thermal mass flow sensors, or thermal gas flow meters. The thermal mass flow meter is a meter that uses the principle of heat transfer to detect flow.
That is, the measurement is performed based on the heat exchange relationship between the flowing fluid and the heat source (the object heated outside the fluid or the heating body outside the measuring tube).
The main measurement gas. Thermal gas mass flow meters are mainly divided into two categories, namely: thermally distributed and immersed (or plug-in).
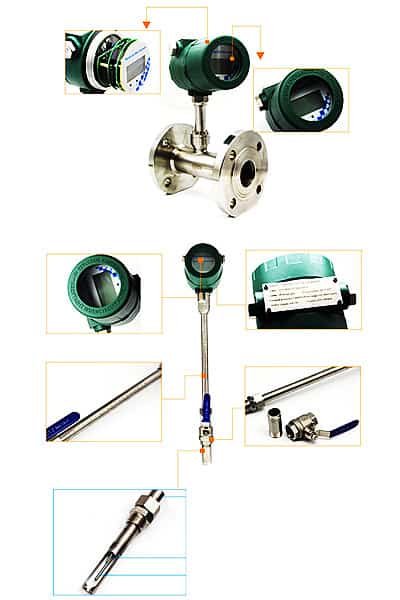
Thermal mass flow meter working principle
Thermal gas mass flow meter is designed on the basis of thermal dispersion. And adopts method of constant differential temperature to measuring gas flow. It has advantages of small size, easy installation, high reliability and high accuracy, etc.
The meter contains two platinum resistance temperature sensors. The thermal principle operates by monitoring the cooling effect of a gas stream as it passes over a heated sensor. Gas flowing through the sensing section passes over two sensors. One of which is used conventionally as a temperature sensor, whilst the other is used as a heater. The temperature sensor monitors the actual process values whilst the heater is maintained at a constant differential temperature above this by varying the power consumed by the sensor. The greater the gas velocity, the greater the cooling effect and power required to maintain the differential temperature. The measured heater power is therefore a measure of the gas mass flow rate.
The format of gas velocity and power is shown as below:
Where:
- ρg is the specific gravity of the medium
- V is velocity
- K is the balance coefficient
- Q is heater power
- Δ T is a differential temperature
- The medium temperature range of the meter is -40℃~220℃.
In the format (1), the specific gravity of medium is related to the density:
Where:
- ρg is the medium density in working condition(kg/m3)
- ρn is the medium density in standard condition, 101.325kPa, and 20℃ (kg/m3)
- P is the pressure in working condition(kPa)
- T is the temperature in working condition (℃)
In the formats (1) and (2), there is a certain functional relationship between the velocity and pressure in working condition, medium density, the temperature in working condition.
Due to the sensor temperature is always 30℃ higher than the medium temperature (environment temperature), and the meter adopts the method of constant differential temperature, therefore the meter do not need to do temperature and pressure compensation in principle.
Guess you like: What is Reynolds number?
Know more about How Thermal Mass Flow Meter Technology Works?
Video source: https://www.youtube.com/watch?v=YfQSf2NBGqc
Thermal mass flow meter applications
The thermal measuring principle is widespread in the industry, and is being used successfully in many applications with gas flow, for example:
- Oxygen, nitrogen, hydrogen, chlorine, and multi-component gas measurement.
- Blast furnace gas and coke oven gas measurement.
- Flue gas measurement.
- Aeration and chlorine measurement in biogas and water treatment.
- Compressed air measurement.
- Gas flow measurement for natural gas, liquefied gas, flame gas, etc.
- Primary air and secondary airflow measurement of power plant blast furnace
- Flow measurement of underground ventilation or exhaust system
Further reading: Industrial LPG/Propane flow meter
Thermal mass flow meter advantages
- No need for temperature and pressure compensation for gas flow measurement. Convenient and accurate measurement;
- Wide range ratio, can be used for gas leak detection;
- Measuring flow rate range: 0.1Nm/s~100Nm/s.
- Good seismic performance and long service life, free from the influence of vibration on measurement accuracy;
- Overall digital circuit measurement, accurate measurement and convenient maintenance;
- Using RS-485 communication, factory automation and integration can be realized. click for inqueries
- No pressure loss, suitable for pipes of any shape with known cross-sectional area.
- Corrosion-resistant sensor, suitable for measuring corrosive gas.
- It is especially suitable for large-caliber measurement to ensure the accuracy of measurement and is suitable for trade settlement.
- The amount of construction is very small. Due to the plug-in structure, it can be installed and maintained online.
- The base-type instrument can display on-site and control with alarm.
Thermal mass flow meter disadvantages
- The thermal mass flow meter responds slowly.
- Places where the measured gas composition changes greatly. Due to changes in the cp value and thermal conductivity, the measured value will vary greatly and cause errors.
- For small flow, the meter will bring considerable heat to the gas to be measured.
- For thermally distributed thermal gas mass flow meters, if the measured gas deposits a scale layer on the pipe wall, the measured value will be affected. Must be cleaned regularly. The thin tube type instrument has the disadvantage of being easy to be blocked, and it cannot be used under normal circumstances.
- The use of pulsating flow will be restricted.
- Thermal mass flow meters for liquids are also restricted in the use of viscous liquids.
Read more about: Benefits Of Digital Gas Mass Flow Meters
Extended reading:
What is the K-factor in a flow meter?
Cryogenic Flow Meters|Liquid Nitrogen-Liquid Oxygen-LNG fluids
FAQ
Guess you like: What is Reynolds number?
Related Products:
Sino-Inst offer over 10 Thermal Mass Flow Meters, with Best Price.
A wide variety of Thermal Mass Flow Meters options are available to you, such as free samples, paid samples. All of our flow meters can work with the AMS NEW TREX. About 13% of these are magnetic flow meter. 14% are Insertion Magnetic Flow Meter. 25% are Venturi flow meter. 13% are Handheld ultrasonic flow meter, and others are Liquid Turbine Flow Meters.
Sino-Inst is Thermal Mass Flow Meter suppliers, located in China. Mass flow meter products are most popular in North America, Mid East, and Eastern Europe.
The United States, and India, which export 99%, 1%, and 1% of Thermal Mass Flow Meter respectively.
You can ensure product safety by selecting from a certified supplier, with ISO9001, ISO14001 certification.
Wu Peng, born in 1980, is a highly respected and accomplished male engineer with extensive experience in the field of automation. With over 20 years of industry experience, Wu has made significant contributions to both academia and engineering projects.
Throughout his career, Wu Peng has participated in numerous national and international engineering projects. Some of his most notable projects include the development of an intelligent control system for oil refineries, the design of a cutting-edge distributed control system for petrochemical plants, and the optimization of control algorithms for natural gas pipelines.